デジタルファクトリー・製造IoT
今や製造業においても、グローバル化の深化、団塊世代のベテランの退職等に対応するためにデジタル・マニュファクチャリングの推進が不可欠となっています。また、外部環境の変動激化やグローバル競争の激化などから、製造部門全体の生産性を向上するためにもアナログから脱却し、デジタル化していくことが必須となっています。
当社では、これまでの様々な製造業でのサポートを通じた豊富な知見を基に、クライアントが抱える課題を明確化し、ものづくりにおける最適な製造IoTプラットフォームの構築を通じて、デジタルファクトリーの実現を支援いたします。
デジタルファクトリー・製造IoTの必要性
デジタルファクトリー・製造IoT等のデジタル・マニュファクチャリングを実現・実施することで、以下のように、デジタルデータを活用し、企業の生産性を上げるとともに消費者が求める製品を製造することが可能になります。
①人手不足・ベテランの退職という課題に対し、匠の技に頼っていた人的作業の機械化を推進
②製造現場の情報をグローバルで共有し、組織全体の生産性を向上
③販売やアフターマーケットのデータから、よりタイムリーに消費者のニーズにマッチした製品を製造
しかしながら、目的を明確にしないまま取り組んでしまうと、情報を取得しても何も活用されないままになってしまいます。
デジタル化を活用して製品・サービス、もしくはその製造方法をどう進化させるか、経営的(ビジネス的)にどのようなイノベーションを目指したいのか、を事前に現場の実務層だけではなくマネジメント層を巻き込んで、議論しておくことも重要です。
【図1】製造工程のデジタル化
製造IoTプラットフォームを構築するうえでの重要視点
製造IoTプラットフォームの導入においては、サプライチェーン全体を俯瞰した拠り所となるデータモデルの定義が重要になります。そのうえで、グローバルでの標準化に向けて、各工場におけるデータの標準化・規格化を推進することが必須となります。
さらに今後は、自社工場だけではなく、重要な協力パートナーを巻き込んでデータを収集・蓄積したうえで、活用を行っていくことが重要です。
①データモデルの定義
②グローバルでの標準化
③サプライヤーへの展開
データモデルの定義
データモデルの定義のためには、QCDごとに目指すべき到達点を明確化したうえで、そのために必要なデータを整理する必要があります。
例えばQ(品質)については、目指すべき到達点としての最終目的を「製品品質の向上」と定義したうえで、さらに「モノ自体の保証」と、「モノづくりの保証」という2つのテーマに細分化できます。その2つのテーマごとに必要となる具体的なデータ項目を定義していきます。
このように、QCDごとに目指すべき到達点を明確化し、その到達地点を目指すための検討テーマを抽出。そのテーマごとに必要とするデータ項目を定義していくことが重要です。
QCDごとに定義したデータ項目について、実際の工程を確認しながら下記3つの視点でデータモデルの作成を行います。
- 業務視点:業務としてどこで、どのように使うのかを明確化
- データ視点:すでに取得可能なデータなのか、どのようにすれば取得できるのかを明確化
- 将来活用視点:自動化、電動化等、ものづくりの変化が生じるため、それらに対する対応策も同時に明確化
【図2】データモデルの定義
グローバルでの標準化
工場は、その設立経緯や歴史によって、マネジメント・インフラ・業務のレベルが異なります。
- マザー工場である国内の工場
- 旧来の設備・手法の海外工場
- 買収で手に入れた工場
結果として、各拠点から得られるデータの粒度・精度・頻度が変わります。データの定義が拠点ごとに異なると、全社として横比較や意思決定を逸するリスクが出てしまいます。
そのため、グローバルで標準化されたデータモデルでデータの蓄積を行うことが重要です。
また、実際に各工場に関し統一化されたデータモデルを展開する場合、各拠点横並びで同じ進め方をしていては、各拠点ごとの素地となる管理レベルが異なるため、実現時期にバラつきが出てしまいます。
そうすると、マネジメント層が求めるスピードでの実現は難しいものになります。
各拠点の実力を認識したうえで、
①現状取得可能なデータ
②必須で取得すべき情報
③業務高度化に向け取得すべき情報
と優先順位を付けて整備を行っていくことが重要です。
サプライヤーへの展開
今日のものづくりは、自社の1社だけでは到底成り立ちません。生産を委託する協力会社、原材料/部品の購入先等の協力が必須です。
製造IoTプラットフォームの構築を考えた場合に、自社工場内の情報に留まらず、生産委託先・購入先との連携を行うことが重要です。
さらに今後は、
①設計に関する情報⇒協力会社・仕入先
②販売・出荷・物流に関する情報⇒物流会社
③製造に関する情報⇒顧客
と情報の連携をすべき対象範囲が拡大することも予想されます。
今までのように担当者間の情報連携では、物流会社や顧客と情報連携を行うには限界があります。
自社と対象会社との間で共通の情報基盤を整理し、それぞれの情報を逐次共有し、最適なサプライチェーン構築に向けたアクションを共に検討していくことが重要です。
レイヤーズの製造IoTプラットフォームの構築ステップ
IoTのツール等を導入する前に、データの標準化、インフラ仕様の標準化を推進していく必要があります。
特に各拠点・各工程で収集しているデータそのものが異なっていたり、データ項目やデータの精度、コード体系等も様々です。そのため、全社活用を行っていくためにはデータの標準化・規格化は必須の項目です。ただ、データの標準化・規格化に囚われ過ぎると、効果発現が遅くなってしまいます。
標準化・規格化を進めつつも、今あるデータを前提とした活用方法を検討し、一旦は収集蓄積を行っていく環境整備を優先的に実施(=CanBe)。収集蓄積したデータを積極的に活用し、全社のデータリテラシーを向上させながら、データの標準化やデータの精度を求めていくことが重要です。
【図3】製造IoTプラットフォームの構築ステップ
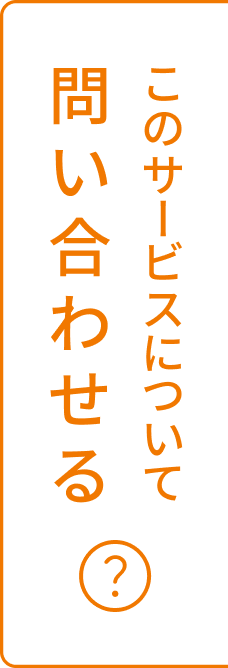
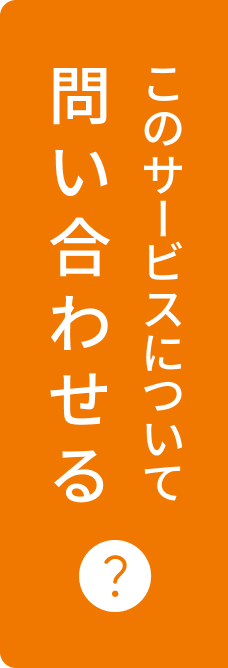
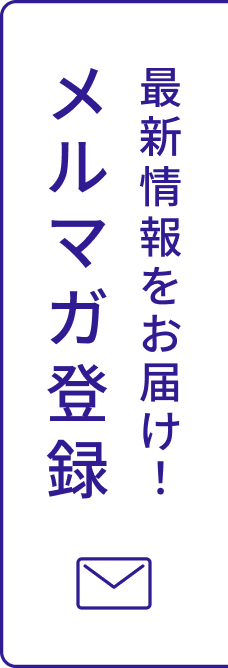
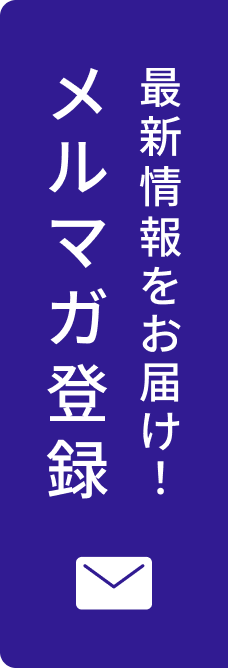
問い合わせる問い合わせる メルマガ登録
最新情報をお届け! メルマガ登録