自動車部品メーカーにおける原価企画体制の再構築
クライアントが抱えていた課題
SOP(スタート・オブ・プロダクション)前の製品開発フェーズにおける目標原価管理と、SOP後の量産原価管理のそれぞれに課題を抱えていました。
原価企画の担当部署は、システムを使用せず、手作業で目標原価・見積原価の計算を行っていました。また、計算のための情報もシステムに頼らずに収集していました。そのため、業務が属人化し、担当者でなければ目標原価設定根拠の確認や見積原価計算結果の修正ができないという状況でした。
量産原価については、計算完了・経営層への報告に日数を要することが大きな課題でした。同社はグローバル利益向上に向けた活動を推進しており、経営層は得意先別、車種別、バリエーション別などの収支(損益)情報がスピーディーに入手できる仕組みを求めていました。精緻でなくてもいいので、意思決定の材料となる情報をなるべく早く得たいという要望でした。
目標原価と量産原価が比較できないことや手作業による計算だったため、営業/調達部門などと原価情報を共有できないことも課題としていました。
レイヤーズのアプローチ
目標原価管理について、以下のような業務変革・原価データベース(DB)の構築を進めました。
- 「目標原価」/「組織別コストダウン目標」の早期設定・展開・部門間合意形成
- 時点のリアルタイムな原価状況(見積原価)/原価アイテムを加味した将来的な原価(原価見通し)の見える化
- 「組織別コストダウン目標」を意識した原価低減活動の推進・達成状況/未達要因の見える化
- コストにかかわるゲート会議体(コストレビュー)の新設
- プロジェクト原価情報、コストダウンノウハウの一元管理・他車種活用
量産原価管理については、収支実績管理システムを導入し、得意先別、車種別、バリエーション別などの損益情報が把握できる環境を整えました。
【図1】原価企画システム全体像
成果
目標原価管理については、上記の変革の他に、過去車種・部品コスト情報の活用、コストダウンアイテムDBを用いた原価低減ノウハウの蓄積・横展開などを実現しました。
量産原価管理については、原価低減や市況変動などの売上変動要因、設計変更や為替変動などの材料変動要因による影響額をひと目で把握できる情報を経営層に早期に提供できるようになりました。
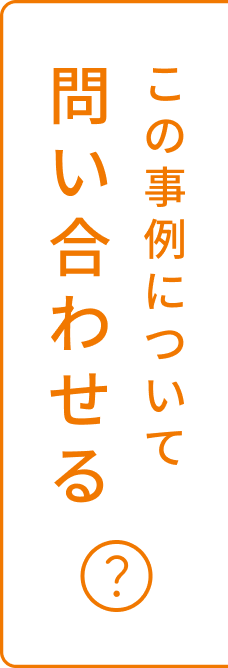
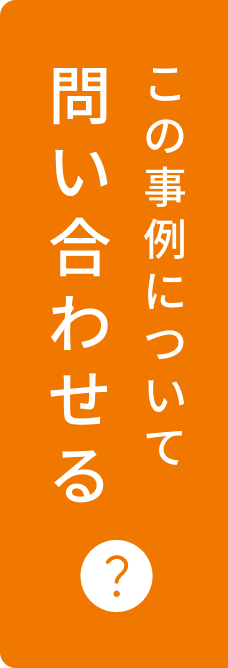
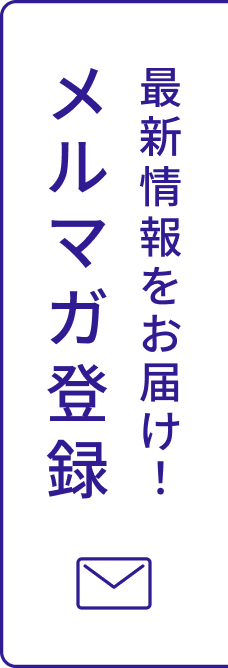
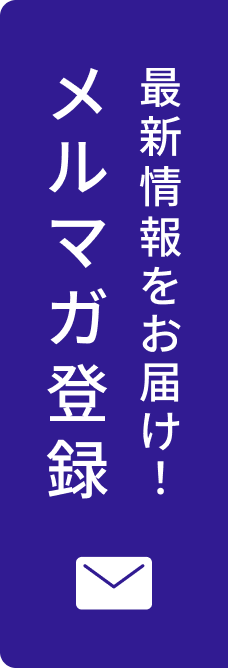
問い合わせる問い合わせる メルマガ登録
最新情報をお届け! メルマガ登録