自動車部品メーカーにおける新原価管理制度・
システムの構築と導入
クライアントが抱えていた課題
国内拠点・グローバル各社で原価計算方法がバラバラであり、製品別の原価の妥当性が判断できていませんでした。また、業績管理においても各拠点の進捗や課題が同じ基準で管理できないという課題をクライアントは抱えていました。
現場改善や現場での取り組みが原価に反映されず、効果測定ができませんでした。また、直接原価以外の費用はまとめて一つの配賦基準で製品に賦課されたため、費用の適正化や改善対応が取れませんでした。
急激な円高に対して各社海外展開を進めましたが、海外で作ると本当に安く作れているのか、客観的な尺度がありませんでした。
レイヤーズのアプローチ
グローバルで最適な連結経営をするための「見える化」とインフラ整備を掲げて、(1)極ごと(拠点ごと)の原価比較ができる、(2)原価管理を強化する、の2つを目的に以下のテーマで改革に取り組みました。
- 同一原価計算方法、同一尺度で比較を可能にするための原価の世界基準の設定
- 基準原価(目標原価)との対比による課題の見える化による原価低減の促進
- 品番別原価の正確性向上のための活動実績原価計算(ABC原価計算)の導入
- 管理サイクルのスピード化のための品番別日次原価管理とライン別利益管理の導入
- 上記を実現する全拠点共通情報システムの企画・構築から導入、立ち上げまでの支援
【図1】アプローチ方法
成果
原価管理については、すべての拠点が同じ基準・方法で日次の製品別の原価を計算し、拠点間、あるいは同一拠点内の製造工程間、さらには組織間での比較を可能にし、健全な競争を促しながら、原価低減を継続的に追求する体制が実現しました。
利益管理については、システムの活用によって利益責任主体別業績が明らかになったとともに、経営から現場まで同一尺度の数値根拠を持って議論できるようになり、タイムリーな目標利益必達に向けた課題抽出、原因分析、対策検討・実施のPDCAサイクルが確立されました。
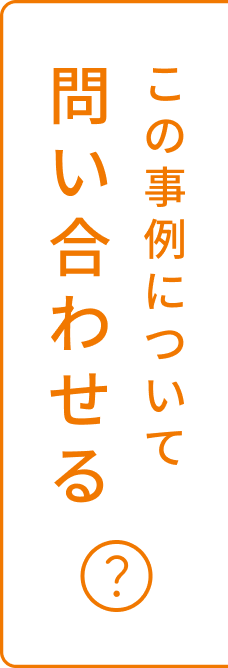
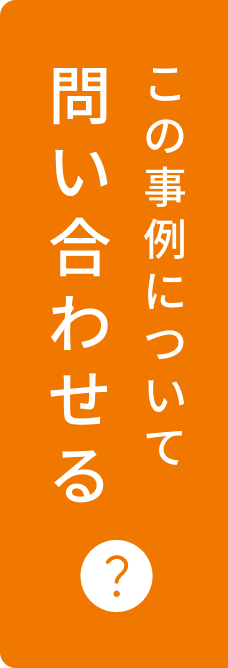
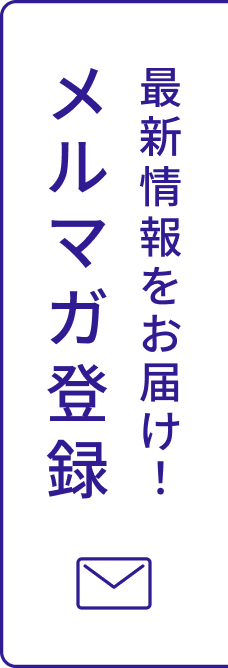
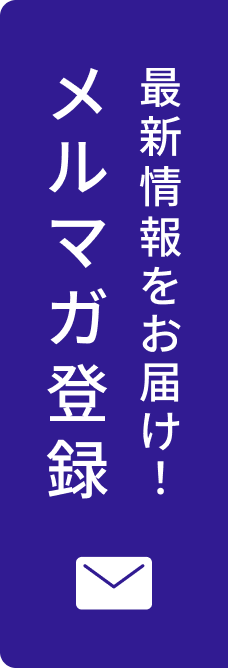
問い合わせる問い合わせる メルマガ登録
最新情報をお届け! メルマガ登録