その製品、赤字かも!?
経営者が知るべきライフサイクル利益・コスト
これら環境変化を契機に、以前から課題認識されていた製造業におけるサプライチェーン再構築やものづくり変革(設計・製造のデジタル化など)が加速していますが、それら投資はコスト増へとつながるため、場合によっては価格競争力を失いかねません。
従って、今まで以上に「コストダウン・コストコントロール」が重要となっています。
本稿では、そのような有事の時代においても利益を出し続けるための、企画・開発から製造、アフターサービスまで含めた製品ライフサイクルでの利益・コスト管理のポイントを解説いたします。
利益・コストをコントロールできない会社は生き残れない
新型コロナウィルスの世界的流行は、日本国内において2022年8月までに累計で3,906件の企業倒産をもたらすなど、大打撃を与えました(出典:帝国データバンク)。
特に製造業においては、半導体などの重要部品の供給が需要に追いつかず製品を製造・出荷できなくなるなど、サプライチェーン上の危機に陥ることとなりました。
【図1】日本国内企業 新型コロナウィルス関連倒産件数(出典:帝国データバンク)
また、2022年のウクライナ危機においても、エネルギーの価格高騰やサプライヤ供給網の寸断など、再び製造業に対するダメージを与えています。
このような状況下で、各企業はサプライチェーンの再構築など、以前から認識されていたものの対策実行に至っていなかった課題に取り組まざるを得ない状況となりました。
しかし、危機を打開するために安易に様々な対策に取り組むとコストアップを招き、企業をさらなる窮地へ追い込むことになりかねません。
例えば、サプライヤからの部品の安定供給を企図して複数社購買を行った場合、購入量のスケールメリットが低下することで購入単価の上昇を招いたり、複数のサプライヤを管理するための間接費がかかることで、かえってコストアップにつながる可能性があります。
また、製品の製造・出荷におけるリスクを低減するために、製造拠点を先進国あるいは日本に移管させた場合、労働賃金の上昇によって結果的にコストアップとなりかねません。
これら対策が誤っているというわけではありませんが、合わせてコストダウン・コストコントロールを行っていかないと、結果としてコスト競争力を失う可能性もあります。
今後はより一層、コスト競争力を持つ企業こそが生き残る状況であると言っても過言ではありません。
製品ライフサイクル利益・コスト管理とは?
自社が、競合他社と比較して真にコスト競争力を持っているか、あるいは自社製品がどれだけ利益を創出できているか把握・管理する方法として、製品ライフサイクル利益・コスト管理をご紹介します。
製品ライフサイクル利益・コスト管理とは、製品の企画・開発からアフターサービスまでの全ての売上とコストを製品に紐づけることで把握できる「製品が生涯にわたって稼ぐ利益」を管理することにより、製品ライフサイクルにおける利益最大化を目指す管理方法です。
【図2】製品ライフサイクル利益・コスト管理とは?
管理のポイントとして、次の3点が挙げられます。
① 製造原価だけでなく、開発、販売、サービスコスト含めた全体コストを対象とする
これまでコストと言えば製造原価ばかりに着目されていましたが、現在は開発・販売・アフターサービスなどのコストが企業のコスト全体に占める割合が高まっているため、製造原価以外も含めた全体コストをコントロールする必要があります。
② コストと同時に売上を把握し、利益の最大化を図る
コストと同時に売上も把握することでライフサイクル全体の利益を可視化し、コストコントロールに加えて売上のコントロールも行い、ライフサイクル利益の最大化につなげます。特に近年は製品売り切りのビジネスではなく、アフターサービスが収益源となっているビジネスも多いため、製品販売~アフターサービスの売上を製品に紐づけて把握することが重要です。
③ 会計期間ではなく、製品のライフサイクルで管理する
一般的には年次/半期/四半期/月次などの期間損益で業績管理を行うことが多いですが、製品ライフサイクルが長いビジネスであればあるほど、期間損益だけでは中長期的に儲けるための事業/製品戦略やビジネスプランを描きにくいため、「会計期間」だけではなく「製品ライフサイクル」で損益管理することも重要となります。
製品ライフサイクル利益・コスト管理の「5つの活用局面」
製品ライフサイクル利益・コスト管理には、製品の企画・開発~生産・販売中止までの流れにおいて、次の5つの活用局面があります。
①ビジネスモデルに応じた利益設計
企画・開発段階において、たとえば従量課金へのシフトなど、ビジネスモデルの変化に応じたライフサイクル全体の売上とコストを予測しながらライフサイクル全体の利益設計を行います。
②開発コスト管理、原価企画/原価管理、販管費管理、サービスコスト管理によるコストダウン
近年増加傾向にある開発コストの適正化や原価企画活動における製造原価の作り込みなど、開発~アフターサービスに至る各段階において、徹底的にコストダウンを図ります。
③適正価格設定と値引コントロール
ライフサイクル利益・コストを踏まえて、顧客・チャネル別の利益と提供形態(単品/セット売)等にもとづく価格パターンを設定します。
④サービスビジネスの利益強化
製品の売上だけではなく、購入者に対する保守契約への加入を促したり、保守契約/タイム&マテリアル保守の夫々におけるサービス価格を見直すなどサービスビジネスの利益強化につなげます。
⑤モデルチェンジ方針判断、生産・販売中止判断
ライフサイクル終盤においては、現行機種のライフサイクル利益から見た販売中止や次世代モデルへの切り替え、製品バリエーションの採算性評価をライフサイクル利益にもとづき判断・評価します。
【図3】製品ライフサイクル利益・コスト管理の「5つの活用局面」
ライフサイクル利益・コスト管理の成功の秘訣とは
ライフサイクル利益・コスト管理を成功させるポイントは、次の3つです。
ポイント①: 「誰が、いつ・どう使うの?」と「実行可能性」を最初にみんなで腹落ちする
「誰が、いつ・どう使うの?」
開発・製造・販売・サービスの機能別組織になっていることが多いですが、ライフサイクル利益・コストはそれらを一気通貫で管理する必要があります。各機能はそれぞれの中での最適化を図りますが、経営トップの直下に製品軸の利益・コストを管理する利益責任部門を設置し、機能横串で通すことで製品軸(機能間)での最適化を図ります。
また、活用シーンの例として下記が挙げられます。
- 月次:月次業績管理における製品軸での利益分析と対策 ⇒期間損益管理と連携
- 年次:年度予算/中期経営計画の策定 ⇒期間損益管理と連携
- 商品開発ゲート会議:企画レビューにおける目標設定、設計レビューにおけるコストの作り込み、市場導入後のレビューにおけるモニタリング評価 etc.
「実行可能性」
特に開発コスト・販売コスト・サービスコストは、製品別に把握できていないケースも多くあります。したがって、現行のコストの発生・管理状況を把握した上で、実行可能性を見極める必要があります。
ポイント②:現場にインプット負荷をかけない
開発コストの中でも基礎研究や共通部品の設計にかかるコストや物流コストなど発生コストを製品単位で把握ができないケースも多い中で、現場に製品別工数の記録を強いると猛反発を受けかねません。そこで、多少精度が低くとも既に取得できている実績情報を組み合わせる事により簡易的な数値を算出するなど、現場にとっても納得感のある妥協点を探ることが重要です。
ポイント③:導入に時間・コストをかけない
導入においては、まずは計算・集計のしくみをアジャイル的思想で早期に具現化し、運用しながら自社における管理の仕組みをブラッシュアップしていくことをお勧めします。
最初のステップとしてはExcelなどの使い慣れたツールから始めて、導入範囲の見極めや定常運用の方法などを検討する事がリーズナブルであると考えます。
【図4】実現ポイント(例)
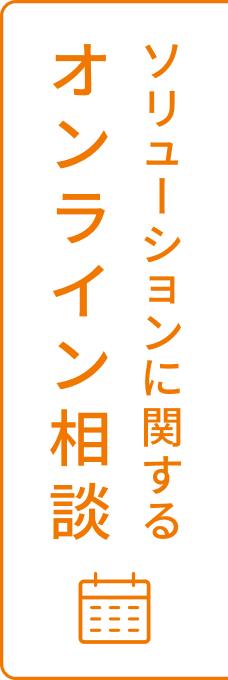
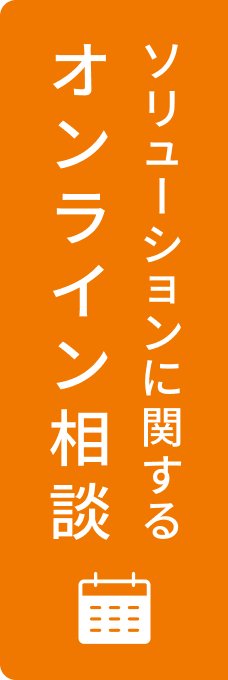
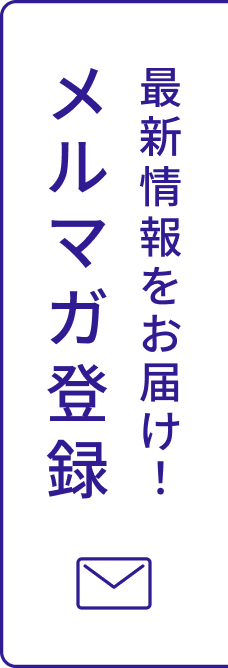
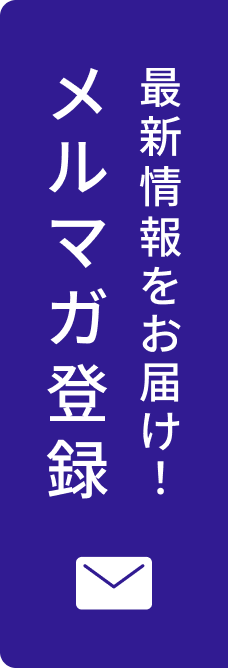
オンライン相談問い合わせる メルマガ登録
最新情報をお届け! メルマガ登録
この記事の執筆者
-
円子 貴義SCM事業部
ディレクター -
小林 真SCM事業部
マネージャー
職種別ソリューション