高収益企業へのスタートライン
~単品別利益管理の実践~
営業利益率20%を目指すためには、更なる高収益化に向けて、単品別(品目、品番、エンドアイテム等受注単位)で利益管理を実施することが必要です。
今回は、利益率向上のための単品別利益管理の実践ポイントと事例をご紹介します。
低営業利益率からの脱却を目指す
一般に利益管理は、製品群別に月次で行われていることが多いですが、これでは利益管理のメッシュが粗く変化点を見逃してしまいますし、気づくタイミングも遅く対応が後手に回ってしまいます。
営業利益率20%を目指すためには、少なくとも製品軸は「単品別(品目、品番、エンドアイテム等受注単位)」、時間軸は「週次、日次」、組織軸は「拠点別(組織の最小管理単位)」での利益管理を目指すべきといえます。当社のコンサルティング実績でも、こうした管理を実践した企業の多くが、利益率の向上を実現しています。
【図1】利益管理の目指すべき姿
製造原価、販売費、一般管理費の実態を掴め
単品別利益管理のためには、まず、製造原価、販売費、一般管理費の実態を掴むことが重要です。
製品の実際原価を掴む
製品の製造原価として標準原価を採用する場合、原価改定が年1回では現在の原価の実力を示しているとは言えません。製品の製造原価は「製造実態をストレートに反映した最新の実際原価」を捉えることが重要です。ここで言う実際原価とは、日々変化する原単位情報を、ダイレクトに製品/工程に紐づけ、タイムリーに計算した原価を言います。従って、標準原価を採用している場合は、標準原価を直近の単品別実際原価を基に毎月改訂するか、単品別実際原価に基づいた原価差異を把握する必要があるといえます。
【図2】原単位とそれに基づく実際原価の把握
IoTをコストマネジメントに活かす
デジタルマニュファクチャリングの取組によって、各種の原単位情報がリアルタイムに取得できるようになってきました。しかし、これらの取組みとコストマネジメントの取組みがまだ十分連動できているとは言えません。例えば、製品の切替えの際に段取り時間を把握しているのにも関わらず、製品別加工費は直接作業時間のみで計算していたりしています。
従って、これらの取組みによって取得できた原単位情報を基に、効率的に単品別製造原価を把握できるようにすることが重要です。
また、こうした日々の原単位情報を把握することにより、実際賃率や実際加工費率等の計算を除き、日々の実際原価を把握することが可能になります。
【図3】製造IoT情報のコストマネジメントへの活用
売上高や直接労務費等による配賦は最小限にする
一般に個々の単品の個別コスト(個別賦課費や直課費と呼ばれる)を十分把握せず、間接費として売上高や直接労務費等で配賦することが多いため、下図のように全ての製品で利益が出ているようになっていることが多く見受けられます。こうしたコスト負担は、売れる製品に多くの費用を負担させる負担能力主義であり、これでは実態にあった利益構造の把握はできません。
売れる製品は相対的に手間がかからず間接費が少ない(原価が安い)、売れない製品は小ロット品など生産効率が悪い(原価が高い)ということは、日常的に感じることです。従って、単品に対する個別コストを把握・直課した上で、間接費や販管費については活動基準原価計算(ABC)を採用して原価・利益の実態を掴むべきです。当社の実績では、売上高や直接労務費等に配賦を出来る限りやめた場合、下図のように売上高下位2~3割の製品が赤字であることが多く、各製品の収益性がより明確化します。
【図4】売上高下位2~3割の製品は赤字
なお、活動原価計算において活動別コストやコストドライバーの日常的に捕捉が実務的に難しい場合は、当社では簡便法として平方根原価計算を採用することを推奨しています。当社の実績では、平方根原価計算での計算結果と活動基準原価計算で計算結果は近似した結果となりますので、是非活用してみては如何でしょうか。
連結一気通貫での単品別利益を掴む
グループで生産や販売を分業している場合、一般に上流の会社から購入したものは、購入原価のみで原価明細が分かりません。これではきめの細かいコストマネジメントはできません。グループ全体のコストマネジメントとしては、それぞれの会社の損益把握だけでなく、連結一気通貫での単品別原価・利益を把握することが重要です。
【図5】連結一気通貫での単品別利益・原価管理のイメージ
連結原価の把握方法としては、
(1)グループ全体を一つの工場とみなし工程別原価計算を繰り返す「連結転がし原価」
(2)連結部品表を使って原価要素を積上げる「連結積上げ原価」
があります。
一般にプロセス型生産形態の場合は「連結転がし原価」、組立型生産形態は「連結積上げ原価」が利用されます。
製品軸、顧客軸、拠点軸の切り口から意思決定に活かす
単品別利益管理において、単に計算しているだけでは意味がありません。単品別損益をベースに製品軸、顧客軸、拠点軸の切り口から、適正な資源配分、アイテムや顧客の拡大・統廃合、コスト削減・利益創出施策等の検討に必要な経営情報を提供し、意思決定に活かすことが重要です。
【図6】単品別利益情報の製品軸、顧客軸、拠点軸でもの活用
また、これらの経営情報を提供するためには、製品×顧客×拠点の最小管理単位での損益を把握する必要があります。連結ベースで単品別利益管理する上では、グループとしての比較可能性を確保するために、これらの多次元軸の定義をグループで統一することが重要です。
【図7】単品別利益管理における多次元分析イメージ
経営計画と実績損益を連動させる
単品別利益管理を徹底させるためには、実績の是非を評価するための単品別利益計画を作成する必要があります。一般に経営計画策定において、単品別に数量計画は立てるものの、利益まで計画していないケースが見受けられます。これでは、計画段階で製品のポートフォリオや統廃合の議論ができません。最新のICTツールを活用すれば、こうした単品別利益計画も効率的に作成できるようになってきておりますので、是非経営計画は単品別までブレイクダウンしてはいかがでしょうか。
また、経営計画策定においては、実績損益管理と連動させるため、下記のようなポイントを考慮すべきです。特に、計画を固定的に考えるのではなく、常に環境の変化に応じて可変的に捉え直していくこと(仮説やシナリオを常に変えられるようにすること)が重要です。
【図8】経営計画と実績損益の連動
マネジメントの連鎖を構築し定着させる
単品別利益を起点としたマネジメントを定着させるために、単品別利益の見える化に合わせ利益マネジメント方針を明確化するとともに、下記のような利益創出のためのマネジメントの連鎖を構築する必要があります。マネジメントの連鎖の構築に当たっては、「計画→実績・進捗管理というビジネス・マネジメント系」と「コミットメント→業績評価というヒューマン・モチベーション系」の両面から構築することが重要です。こうすることにより、組織が常に利益を意識したマネジメントを実践できるようになります。
【図9】利益創出のためのマネジメントの連鎖
食品メーカーにおける単品別利益管理
ある食品メーカーでは、新製品の発売数の増大に伴い、商品打ち切りや拡売費の増大などを招き、営業利益が低下傾向にありました。営業利益は製品群別には出していましたが、それだけでは経営判断に限界を感じていました。そこで、単品別利益を製品軸、顧客軸(1次、2次、小売)、拠点軸(工場、営業所)で出す単品別利益管理システムを構築しました。単品別利益管理システムの導入により、同一の経営情報を見ながら、営業部門、生産部門、マーケティング部門等が活発に議論し、販売促進施策、コストダウン施策、マーチャンダイジング施策等の見直しがなされ、営業利益率の回復に成功しています。
以上のように単品別利益管理は、利益管理のスタートラインです。先ず、これが出来て初めて営業利益率10%以下から脱却できる素地ができたと言えます。単品別利益管理の詳細については、是非、お問い合わせください。皆様と一緒に営業利益率20%を目指していきたいと思っております。
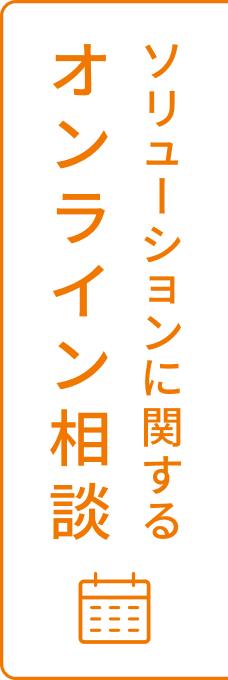
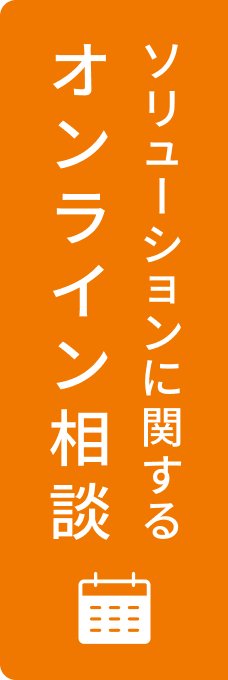
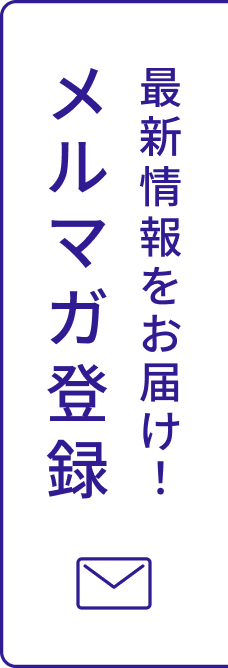
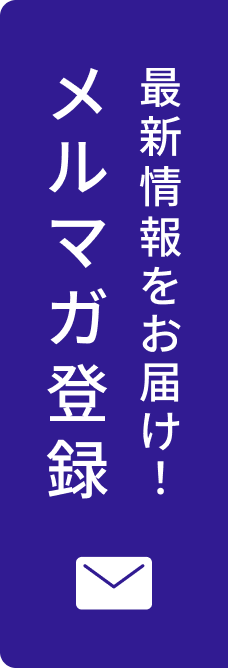
オンライン相談問い合わせる メルマガ登録
最新情報をお届け! メルマガ登録
この記事の執筆者
-
上山 吾郎経営管理事業部
マネージングディレクター -
村井 泰三経営管理事業部
バイスマネージングディレクター -
石原 潤経営管理事業部
マネージャー
職種別ソリューション