脱「昭和の原価計算」
~コストマネジメントをアップデートする~
今回は、こうした伝統的な原価計算を振り返りながら、その後の新しいコストマネジメントの取組みをご紹介します。
昭和の原価計算からコストマネジメントのジャングルへ
日本の制度会計で認められる原価計算は、昭和37年(1962年)制定の「原価計算基準」に準拠した原価計算ですから、前述の通り60年以上時が止まったままです。
しかし、管理会計として利用されるコストマネジメントは様々なものが考案され、ジャングル的様相を呈しています。
即ち、管理会計としてのコストマネジメントは、意思決定に利用されるため様々な方法論があり、一概にこれがベストとは言い切れません。それぞれの特徴を考慮しながら、自社の目的に適したものを活用すべきと考えます。
今回は、「原価計算基準」に準拠した伝統的な原価計算(昭和の原価計算)として代表的な下記をご紹介します。
(1)実際個別原価計算、(2)実際総合原価計算、(3)標準原価計算、(4)直接原価計算
また、新たなコストマネジメントとして様々なものが考案されてきましたが、今回は当社のコンサルティングで活用している下記をご紹介します。
(5)実績原価計算、(6)活動基準原価計算(ABC)、(7)スループット会計、(8)リードタイム・コスティング、(9)ライフサイクル・コスティング、(10)平方根原価計算
伝統的な原価計算(昭和の原価計算)とは、どんなものか
伝統的な全部原価計算とそれが採用される販売生産方式は、一般に下記のようになります。制度会計上は、各社のビジネスモデルに応じて、(1)実際個別原価計算、(2)実際総合原価計算、(3)標準原価計算のいずれかを採用していると言えます。
(1)実際個別原価計算 | (2)実際総合原価計算 | (3)標準原価計算 | |
---|---|---|---|
一品一様品の受注生産 | 〇 | - | - |
規格品の受注生産 (受注ロット別に計算) |
〇 | - | 〇 |
規格品の見込生産 (生産ロット別に計算) |
〇 | - | 〇 |
規格品の見込生産 (品番別に計算) |
- | 〇 | 〇 |
自家建設 (固定資産等) |
〇 | - | - |
スクロールできます >>
【図1】実際個別原価計算、実際総合原価計算、標準原価計算の比較
(1)実際個別原価計算とは
実際個別原価計算は、「1単位の製品」あるいは「バッチないしロットとして製造する一定数量単位の製品」に対し、製造指図書を発行し、指図書別に製造原価を集計する原価計算方法です。一品一様の製品だけなく、規格品(組立型生産プロセス、装置型生産プロセスのいずれでも)でも採用されます。
製造指図番号 | No.100 | No.101 | No.102 | 合計 | |
---|---|---|---|---|---|
前月繰越 | 1,000,000 | 400,000 | 1,400,000 | ||
当月製造費用 | 材料費 | 800,000 | 800,000 | ||
補助材料費 | 100,000 | 200,000 | 300,000 | ||
プレス加工費 | 100,000 | 400,000 | 500,000 | ||
組立加工費 | 1,800,000 | 1,600,000 | 3,200,000 | 500,000 | |
合計 | 1,900,000 | 1,900,000 | 1,200,000 | 4,800,000 | |
次月繰越 | 0 | 2,300,000 | 1,200,000 | 3,500,000 | |
当月完成品 | 2,900,000 | 0 | 0 | 2,900,000 |
スクロールできます >>
【図2】実際個別原価計算の計算概要イメージ
(2)実際総合原価計算とは
実際総合原価計算は、一般に装置型生産プロセスの業界において多く採用される原価計算方法です。総合原価計算では、工程別に計算が行われるため、転がし原価計算とも言われています。
実際総合原価計算は、操業度や生産ロスが変動する企業で適した原価計算と言えます。
【図3】実際総合原価計算の計算概要イメージ
また、実際総合原価計算には、前工程費の内訳を持たない「累加法」と内訳を持つ「非累加法」があります。以前は計算が簡便な「累加法」が採用されていましたが、最近はICTの進歩により複雑な計算がスピーディにできるようになったため「非累加法」が採用されるようになってきています。
(3)標準原価計算とは
標準原価計算は、一般に組立型生産プロセスの業界において多く採用される原価計算方法です。特に購入材料、購入部品の占める割合が多く、生産ロスが安定的な企業で適した原価計算方法と言えます。標準原価を計算するためには、部品表や作業標準表(工程手順表)等を使って下図のように積上計算を行います。
【図4】標準原価計算の計算概要イメージ
標準原価計算においても、実際原価は計算され、標準原価と実際原価の比較分析によって生産性を評価しコストコントロールを行っていきます。
(4)直接原価計算とは
直接原価計算は、総合原価計算において製造費用のうち変動直接費および変動間接費のみを製品の直接原価として計算し、固定費を製品に集計しない原価計算方法です。固定費が大きく操業度が変動する企業において適した原価計算と言えます。
制度会計で直接原価計算を利用する場合は、会計年度末においては、当該会計期間に発生した固定費額を期末の仕掛品および製品と当年度の売上品とに配賦する必要があります。従って、直接原価計算は、制度会計よりも、各種の収益性分析や各種のシミュレーション等の「意思決定のための原価計算方法(管理会計)」として多く活用されています。
【図5】直接原価計算の計算概要イメージ
新たなコストマネジメントの行方
新たなコストマネジメントは、各種目的に応じて考え出されてきました。今回ご紹介する方法以外にも様々な方法があると思いますが、今回は当社のコンサルティングで活用している方法をご紹介します。
(5)実績原価計算とは
実績原価計算は、標準原価計算において部品表や作業標準表(工程手順表)等を使って下図のように積上計算を行う考え方を利用し、単価・消費数量・賃率・作業時間・歩留等の原単位を実際の数値に置き換えて積上計算を行う考え方です。標準原価計算を採用している企業で、原価差異分析を詳細に行う場合に適した原価計算といえます。
【図6】標準原価計算との比較した実績積上原価計算の計算概要イメージ
通常、実績原価計算では実際の原単位はその時の最新の実績値を利用します。しかし、実際総合原価計算のように月初・月末の仕掛品原価を考慮して計算しないため、厳密な意味での実際原価計算とは言えない点は留意する必要があります。
(6)活動基準原価計算(ABC:Activity-Based Costing)とは
活動基準原価計算(ABC:Activity-Based Costing)は、活動(Activity)単位にコストを集計した後、その活動コストを原価計算対象に集計する原価計算方法です。多品種少量化や自動化等に伴い製造間接費や販売費が相対的に多くなってきましたが、これらの配賦基準が従来のまま直接労務費や売上高等であったことによる反省として導入されています。活動基準原価計算は、段取り等の製造活動だけでなく、物流活動、販売活動、一般管理活動等も対象とします。
【図7】活動基準原価計算の計算概要イメージ
活動基準原価計算は、以前は活動コストやドライバーの捕捉と計算に手間が掛かることから導入を躊躇する企業が多くありました。しかし、昨今のICTの進歩によってこれらの捕捉と計算が容易になり、デジタル時代のコストマネジメント手法として再び注目されており、今後は活動基準原価計算を採用する企業が増えると予想されています。
(7)スループット会計とは
スループット会計は、「スループット(販売価格―直接材料費・外注加工費)の最大化」を目的とし、外部購入費以外の原価(直接・間接の労務費や経費)は業務費用としてプールするだけで、製品別にはあえて配賦しません。スループット会計は、直接原価計算をよりキャッシュフロー的に極めた考え方であり(厳密には原価計算とは言えませんが)、財務会計では資産計上される在庫も、スループット会計では直接材料費として処理します。
【図8】スループット会計の計算概要イメージ
コスト配賦を精緻化する活動基準原価計算とは対称的に、スループット会計は配賦そのものを否定します。スループット会計は、リードタイムの短縮を徹底している企業や、固定費が大きい自動車産業やソフトウェアサービス業の管理会計として利用されています。
(8)リードタイム・コスティングとは
リードタイム・コスティングは、投下資本×リードタイム(L/T)に応じて製造間接費、販売費、一般管理費、資本コストが多く発生するという考え方に基づくものです。具体的には、下図のように投下資本は同じでも、リードタイムが2倍長い製品Bの製造間接費等が2倍高くなると考えます。また、在庫として滞留していても、コストは追加的に負担されていきます。
【図9】リードタイム・コスティングの計算概要イメージ
製品毎のスループットを投下資本×L/Tで割った投資収益率が高い製品を優先して生産・販売することを目指す点で リードタイム・コスティングもスループットに着目していますが、間接費等を製品に負担させていく点ではスループット会計と考え方が大きく異なっています。
リードタイム・コスティングの投下資本としては、「外部購入費」又は「外部購入費+直接労務費」を用います。資本コストとしては、目標ROEの水準である8%程度をベースに設定することを推奨しています。
リードタイムの短縮を徹底している企業や、内製部品を国内で生産するか、海外で生産し日本に移送するかといった最適地生産販売を検討している企業などに有効な考え方といえます。
(9)ライフサイクル・コスティングとは
ライフサイクル・コスティングとは、製品の企画・開発からアフターサービスまでの全ての売上とコストを製品に紐づけ「製品が生涯にわたって稼ぐ利益」の最大化を目指す考え方です。通常の期間損益計算の会計年度を超えた製品軸での利益マネジメント手法ともいえます。
【図10】ライフサイクル・コスティングの計算概要イメージ
一般に、製品企画段階ではライフサイクルでの利益デザインを行う企業は多いですが、製品発売後、終売後のライフサイクルでの実際利益をマネジメントを行う企業は少ないのが現実です。ライフサイクル・コスティングは、特に「製品ライフサイクルが長い」「初期投資が多い」「販売後のアフターサービスで稼ぐ」ようなビジネスモデルに不可欠なマネジメント手法といえます。
(10)平方根原価計算とは
平方根原価計算は、米国Wilson Perumal & Companyが提唱している原価計算です。製品の多様性等の複雑性が増大することによってコストは指数関数的に増大すると仮定して計算します。
具体的には各製品の「コストドライバーの平方根」に基づきコストの配賦計算をします。例えば、販売量が製品A100個と製品B10,000個の場合、従来方式が100:10,000だとすると、平方根原価計算は10:100で配分するので、累積生産量が大きい製品の方が1個当たりの負担額が小さくなります。そうした意味では、平方根原価計算は、経験曲線効果によって累積生産量が多い製品ほど原価が低減することを取り入れた原価計算とも言えます。
【図11】平方根原価計算の計算概要イメージ
当社の経験では、平方根原価計算の結果と活動基準原価計算の結果は近似することが多いため、活動基準原価計算の簡便法として利用しています。
以上のように伝統的な原価計算以外にも様々なコストマネジメント手法が生まれてきていいます。各社の状況に応じて、幾つかの方法を検証してベターな方法を見つけることが大切です。今回ご紹介したコストマネジメントの詳細については、是非、お問合せください。皆様と一緒に新たなコストマネジメントを創っていきたいと考えております。
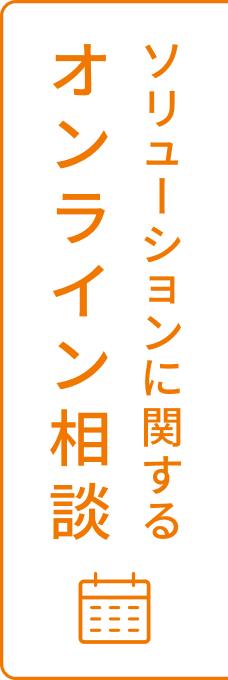
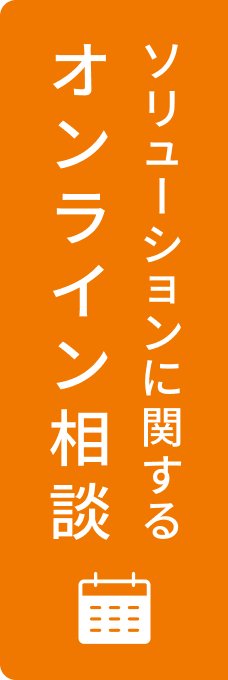
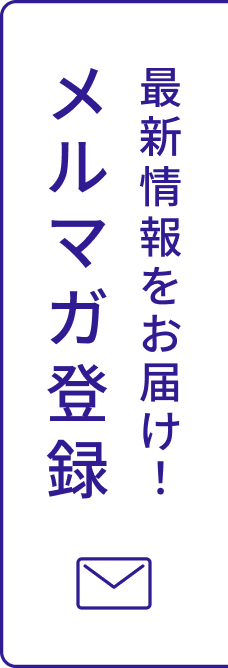
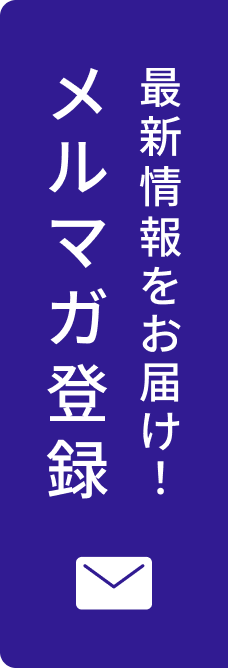
オンライン相談問い合わせる メルマガ登録
最新情報をお届け! メルマガ登録
この記事の執筆者
-
上山 吾郎経営管理事業部
マネージングディレクター -
武貞 正浩経営管理事業部
バイスマネージングディレクター -
田中 貴大ERPイノベーション事業部
シニアマネージャー
職種別ソリューション