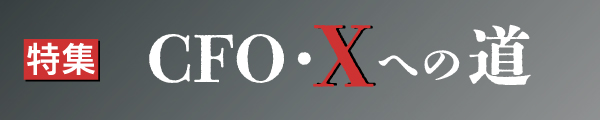
営業利益率20%を目指すには?
~原価管理見直しで低利益体質から脱却~
つまり、資本効率の向上のためには、先ず利益率を抜本的に変革しなければいけません。
そのためには、今の原価管理の方法にメスを入れる必要があります。
今回は、CFOとCFO組織が原価管理・利益管理の専門家として、原価を見直し利益率を向上させるポイントをご紹介します。
【CFO組織とは】
CFOを核に熱き思いと冷徹な計算で企業価値創造をドライブする集団
広くは、経営戦略、経営管理、財務会計、ファイナンス戦略、税務戦略、内部統制、リスクマネジメント、監査、サステナビリティ、IR等の領域を担当
利益管理は細部に至る
皆様の会社に置かれましては、製品軸×地域軸×時間軸でどの程度の粒度で損益・原価を管理されていますか?
当たり前ですが、連結ベースの四半期での損益・原価管理では、「製品MIX」、「最適地生産・生産資源配分」、「顧客分析・販促費戦略」など、なにもかも成り立ちません。もちろん各社の状況によって必要な粒度は異なりますが、基本的に損益・原価管理は細部に至る必要があります。
即ち、製品軸、地域軸、時間軸の観点から目指すべき利益管理・原価管理を実現していくことが重要です。
【図1】利益管理における多次元管理イメージ
製品軸:まずは製品原価を如何につかむか
製品別損益管理の第一歩は、製造原価の実態をつかむことです。製造原価の実態とは、工程の日々の活動がそのまま製品に集約されていくことです。材料単価・消費量しかり、作業工数・機械ショット数しかりです。
その際の原価計算制度は大きく3種類存在します。
1つには、製品別の“転がし”実際原価計算制度です。製品の受入・投入・完成・払出実績により、当該工程の原価を加算していく方法です。この方法の場合は、その結果がそのまま財務会計上の決算数値となり財管一致の原価です。
2つ目は、製品別の“積上”実際原価計算制度です。可能であればその日・その製品の部品表・レシピをもとに、実際の材料単価・消費量・工数等をコストBOMとして登録し積上計算を行います。この方法は在庫が加味されないため、決算数値とは異なる一種の管理会計用の原価であり、財管一致のためには調整が必要となります。
最後に、標準原価計算制度です。一般的に標準原価は、年次ないし半期に予定単価や予定操業度を基に設定されることが多いため、実態と乖離しがちです。標準原価のみで利益管理を行うということは、「今」の意思決定を「1年前」の利益で行うということです。実際転がし法・積上法を採用しない場合には、少なくとも月次での標準原価改定が必要と言えます。
上記3つの方法のどれを取り得るかは、工程の生産情報の充足度合によります。製品の受払なしに転がし法は困難ですし、部品表の設変反映が遅れたり、製造現場判断で代替品を自由に使えたりする状況だと、積上方式は的外れな原価を計算することになります。生産情報をよく調査のうえ、実際原価計算の方式を決めることが重要です。
地域軸:拠点別採算管理から連結一気通貫での製品別利益管理へ
法人として分かれている場合と同一法人内の双方に言えることですが、拠点(工場・工程)別に利益管理を行っていく拠点別採算管理は一般的な手法です。拠点別採算管理は、拠点別に利益目標を設定して計画実績対比をすることで改善を促すだけでなく、最適地生産シミュレーションや投資シミュレーション等の基礎値となります。
ところが、拠点別利益管理を行うと前拠点からの受入は前拠点の利益も含む「材料・部品」となり、製品一気通貫での利益管理の障害となります。単純合算だけでは本当の利益は見えなくなるのです。そこで連結一気通貫での製品原価計算が必要となります。
【図2】連結一気通貫での製品別利益管理
連結製品原価計算の考え方は、前章で記載した“転がし”方式か“積上”方式で製品別に計算することになりますが、品種レベルでの利益管理で意思決定に問題がない場合はP/Lを合算する方式も考えられます。
連結製品原価計算においては、海外を含めた全拠点の生産情報があることが前提となります。多くの企業においては、国内の生産情報整備だけならまだしも、海外の生産情報整備は追いついていません。各拠点の状況を鑑み、生産情報整備が不十分な拠点は「標準原価+原価差額調整」など、ある程度割り切ってしまうことが重要です。
また、勘定科目や原価費目、品目コード等のコードの整備が必要となるため、その状況を認識した上で「コード統一」or「コード変換」の検討を行う必要があります。
時間軸:鮮度と精度のトレードオフをどうするか
製品別利益管理、連結での利益管理の必要性を説明しましたが、一般的にはその集計は月次であり、その集計にややもすれば1か月以上の時間をかけている会社も珍しくありません。
競争環境が安定的な時代においては精度を追い求めることが重要でした。しかしながら、不確実性の高い現在のVUCA時代においては鮮度(スピード)が重要です。この2つはトレードオフ関係にあるため、使用局面に合わせてどのレベル感の利益管理を行うかを検討する必要があります。
【図3】鮮度(スピード)と精度のトレードオフ
時間軸:ライフサイクル利益管理によって見えなかった収益が見えてくる
通常利益管理は、ある会計期間で切り取って集計します。当然ながら、製品によって開発段階のものもあれば、量産が終わりメンテナンス等のアフターサービスの期間のものもあります。その期間だけをとってみても製品の単純比較は難しく、製品ライフサイクルを通した利益管理が重要となります。ライフサイクル利益管理によってはじめて本当の製品利益貢献度がわかり、販売戦略や改善施策にいきてくると言えます。
【図4】製品ライフサイクルでの利益管理
部品メーカーにおける製品別一気通貫損益・原価管理
ある部品メーカーでは、原価は年度改定の標準原価、損益は製品群別の把握となっており、会計情報は決算及び経営報告資料という位置づけで、製品開発の原価企画にも、営業の見積もりにも、製造の改善活動にも使い切れていませんでした。
そこで経理を中心に、開発・営業・生産等のメンバーで損益・原価管理の抜本改革プロジェクトを立ち上げ、まずは他部門における活用用途・必要損益・原価情報を整理し、業務・システムを刷新しました。複数の拠点・子会社を一気通貫で“転がし”原価計算を行うことで連結の実際製品損益を見える化しました。
その結果、原価企画のコストテーブルは実際原価情報で適切にアップデートされ、営業見積もりの精度も改善され、工場での原価低減も当初想定を越えて改善され、現場の活動に役立つ原価管理を実現しました。
以上のように、原価管理・利益管理を再度見直していくことは、低利益体質からの脱却のために不可欠です。まず、これができて初めて営業利益率10%以下から脱却できる素地ができたと言えます。
原価管理・利益管理の見直しの詳細については、是非お問い合わせください。
皆様と一緒に営業利益率20%を目指していきたいと思っております。
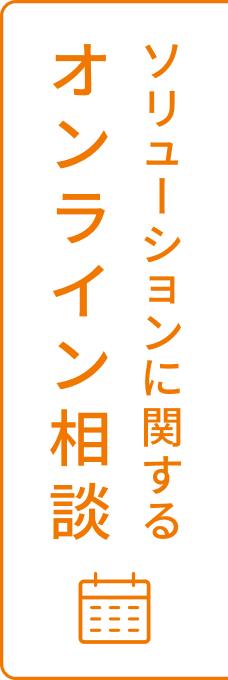
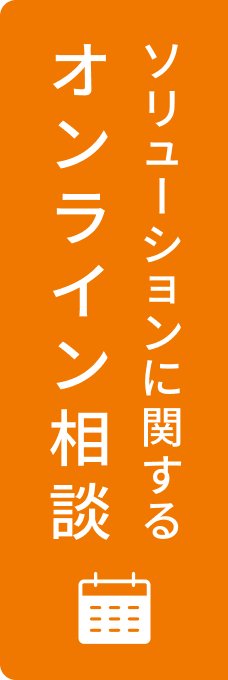
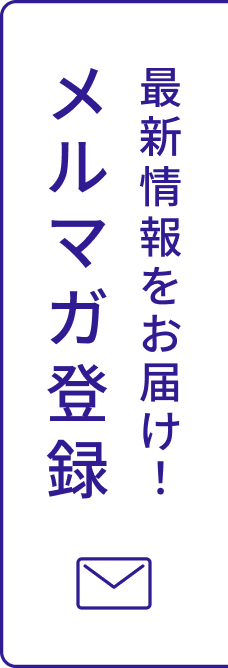
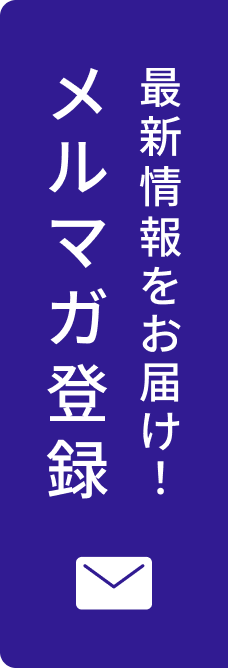
オンライン相談問い合わせる メルマガ登録
最新情報をお届け! メルマガ登録
この記事の執筆者
-
上山 吾郎経営管理事業部
マネージングディレクター -
高橋 俊介経営管理事業部
バイスマネージングディレクター -
石原 潤経営管理事業部
マネージャー
職種別ソリューション