原価差額を見過ごすな!
経営の意思決定に寄与するための製品別実際原価の把握
しかしながら、その意思決定の根幹をなす“コスト”の情報は、旧来から何も変わっておらず、意思決定を行うために十分な情報が提供されていません。
今回は、経営としての意思決定を行うための製品別の実際原価の必要性について解説いたします。
経営の要請に応えられない「原価管理」
経営者の皆様は、自社製品にどれくらいのコストがかかっているかご存じでしょうか?経理部門に問い合わせて返ってくる原価は、自社の最新の実態を表した原価と言えるのでしょうか?
上場企業の多くは「標準原価」を採用しています。一般的には標準原価は、当該会計年度における目指す値を意味しています。そのため改定は年に1回です。中には数年に1回しか改定されない企業も見受けられます。これでは、タイムリーな原価の捕捉はできません。
また、標準原価そのものも製品別ではなく、製品グループ単位や工場単位でしか把握できていないケースも多くあります。各製造拠点における原価定義が異なっていることもあるため、その場合は拠点間の比較もできません。これでは、自社の実態を正確に把握することは非常に困難です。
こういった実態にも関わらず「自社は標準原価を製品ごとに作成していて、改定も少なくとも年に1回は行っているので、適切な意思決定は行えている」と思っている経営者の方も少なくありません。
【図1】標準原価の精度
上記図表は、ある製造業における製品別の標準原価と実際原価を比較したものです。この会社では元より標準原価を採用していましたが、当社にて実際原価の導入を支援する中で、「感覚的に問題がある」と思った製品を選抜し、実際の賃率、作業時間、生産数量等を用いて製品別の実際原価を試算することで、標準原価の精度を検証しました。
どの製品についても実際原価と標準原価との差が大きいことが分かりました。製品Cについては、当初に比べて生産数量が大きく落ちていたので標準原価に比べ180%以上の差異が出ていました。
本来原価情報は、製品の製造拠点を決め、販売価格を設定する等の経営者の意思決定に用いられる情報です。
上述した原価情報では、製品ごとの原価情報の実態を把握できていないため、誤った意思決定を行ってしまう可能性があります。製品別に実際に発生したコストである「製品別実際原価」で、実態を把握した上で意思決定をしていかなければなりません。
製品別実際原価の必要性
標準原価を採用している場合、実際発生費用との差は原価差額という形で現れます。その差が大きければ大きいほど実態と乖離していることになります。しかしながら、製品別に標準原価を設定していたとしても原価差額自体は工場単位/会社単位でしか把握していないことが多く見受けられます。それは、標準原価の目的が財務諸表等の外部に報告する資料に使用することが目的で計算されており、財務諸表には製品別の原価差額を掲載する必要がないからです。
【図2】原価差額の実態
図2のように製品ごとの原価差額が差益・差損で打ち消しあった結果、工場もしくは会社全体で見ると原価差額が少なく見えるケースがあります。しかしながら、製品個々の原価差額を絶対値で集計すると、その差額は非常に大きなものになるにも関わらず、その実態が把握できていない可能性があります。この製品ごとの差益・差損にこそ、業績を大きく改善させる可能性を秘めた、製品個別の課題が隠れているのです。
利益率の向上が至上命題の中で、利益率と同等、もしくはそれ以上の原価差額が生じているのであれば、この隠れてしまった原価差額は見過ごすことのできない大きな問題となるでしょう。
下記は、ある製造業における製品別実際原価把握の事例です。
【図3】販価見直しによる売上拡大事例
この企業では長らく標準原価を採用していました。我々もご支援を行い、実際原価を把握したところ元々設定していた標準原価よりも実際原価の方が安いことが判明しました。実際原価に基づいて販売価格の見直しを行った結果、標準原価ベースの販売価格では利益が出ずにあきらめかけていた大型案件を受注することができました。
このように標準原価では把握できていなかった自社製品の真の姿を把握することで、経営者が適切な判断を下すことが可能になります。
また、現場においても限られた工数・時間の中で、優先的に活動すべき取り組み順位を適切に把握することにも大きな効果があります。
製品別実際原価のポイント
製品別実際原価は、経営としての意思決定に必要不可欠な情報ですが、未だに多くの企業が実際原価を採用していないのは何故でしょうか?
下記の資料は実際原価の構成を図に示したものです。
【図4】実際原価の費目別構成
実際原価では、原則として各費目の原価は、「実際単価」と「実際数量」の2つの実際の原単位情報から算出されます。
- 実際単価:購入単価や賃率等の数量1単位当たりの金額情報
- 実際数量:消費数量や作業時間等の活動の大きさを表す情報
しかしながら、この2つの実際情報を把握するにあたっては、解決すべき問題が多くあります。
実際単価は、モノの価格であれば国境を越えた調達活動のため、為替変動や市場変動を反映した単価にする必要があります。加工費等を表す賃率については、月毎の実際費用と総作業時間を加味して算出しなければいけません。
実際数量は、製品ごとに行われた活動を記録する必要があります。製造現場では製品ごとにラインに投入されている時間を記録し、営業現場ではその製品の商談や見積もりに割いた時間を記録してもらわなければなりません。
このような実際の情報を取得するためには、現場に必要以上の負荷がかかってしまいがちです。しかしながら、これらの情報がなければ精度の高い原価を把握することはできません。IoT機器を用いて可能な限り自動で情報を取得することに加え、経営者自らがリーダーシップを発揮し、実際情報を取得する必要性を説くことが重要です。
次に重要なのは、製造直接費だけではなく、製造間接費や販管費等も含め製品別の原価情報を把握することです。
「材料費や直接労務費等の製造直接費は製品別に把握しているが、それ以外の製造間接費や販管費は配賦しているためブラックボックスになっている」という声を多く聞きます。近年、製造現場における改善活動により製造直接費そのものの割合が少なくなる一方で、製造間接費や販管費は手付かずのまま放置され肥大化している、という状況も見られます。
しかも製造間接費や販管費等は製品別の売上高で配賦するケースも多く見られ、その結果売れ筋商品ほど原価は高く、一方で売上が低迷する商品の原価は安くなってしまいます。しかし、実際原価を算出してみると売れ筋商品程、設備の稼働率が高く、販売促進を行わなくても売れていることから、実際に製品が負担すべき原価は低くなるケースが多くあります。こういったことからも、製造間接費や販管費についても、実態を表さない単一的で因果関係がない配賦ではなく、製品を特定できる費用は可能な限り製品に直課し、直課できない費用については活動を媒介として製品に紐付けて、製品個別の原価を算出することが求められます。
毎日の体重を正しく計測できない人は、ダイエットできない
今まで見てきたように、現状の標準原価では、製品個々の実態を捕捉することはできません。
製造現場で改善活動を行ったとしても、標準原価には現れないため(標準原価に反映されるのは年に1回の更新時)、正当な評価を受けることができません。
「毎日の体重を正しく計測できない人は、ダイエットできない」のと同様に毎日、グローバルで正確な原価を把握できない組織は、原価低減もできません。
経営の意思決定を適切に行うためには、製品個々の活動実態を適切に反映した原価情報、即ち製品別実際原価をタイムリーに把握することが重要です。
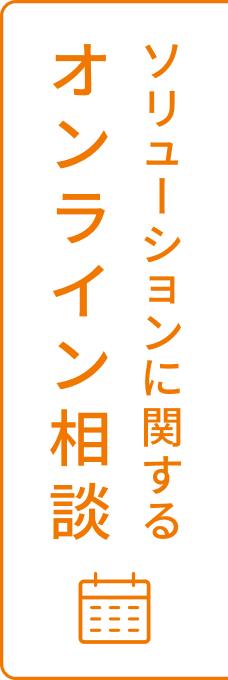
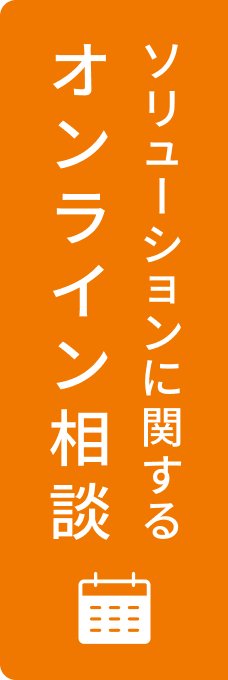
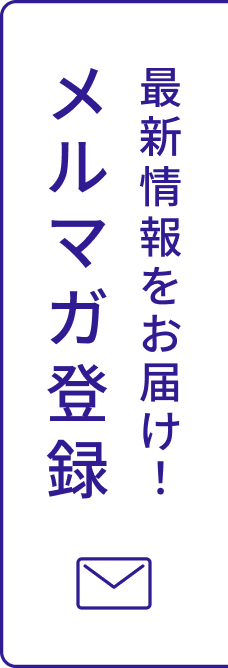
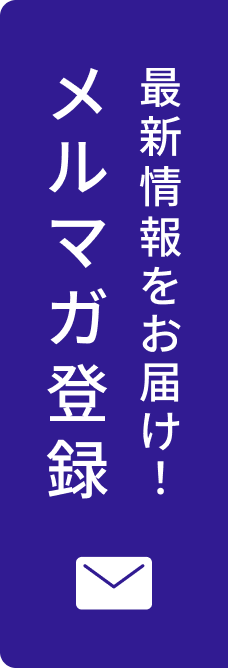
オンライン相談問い合わせる メルマガ登録
最新情報をお届け! メルマガ登録
この記事の執筆者
職種別ソリューション