標準原価のみでは不十分!今必要な原価管理とは
一般的な会社の管理指標として標準原価が利用されています。しかし、多くの場合、標準原価は過去の延長線上から期初に設定されますが、仮に適切・短サイクルで見直したとしても、変動が大きい・先行き不透明な時代では最新の状況を示しているとは言い難く、標準原価による事業判断は大きなリスクを孕んでいると言わざるを得ません。
言い換えると、迅速・適切な意思決定を行うためには、急激に変化する内外要素をストレート且つタイムリーに反映した製品別実際原価が必要となります。
今回は標準原価の限界と実際原価の必要性についてご紹介いたします。
経営層・現場からは不満が続出
多くの企業で原価に関して同様の不満を耳にします。
経営層からは、
- 工場・企画部門から毎月原価報告が上がってくるが、その原価が正しいか確信が持てない。信じて経営判断せざるを得ない。
- 現場の改善報告を積上げるとP/L利益改善額より遥かに大きくなる。しかし、理由が分からず鵜呑みにするしかない。
- 連結全体で利益は出ているものの、どの製品が儲けを生んでいるのかが分からない。
或いは、生産や営業の現場からは、
- 日々コツコツと改善を頑張っている。しかし、経理部門が報告する製品利益は全く改善されていない。
- そのため、自分たちがどれだけ経営へ貢献できているかが分からず、活動のモチベーションが湧かない。
- 製品別原価が工場現場の実感とあまりに大きく乖離している。(特に加工費や間接費)
- 他社とスペックの差はないのに自社製品の原価はなぜか高い。その原因を特定できない。
といった内容です。
何故、このようなことが生じてしまうのでしょうか。
様々な理由がありますが、1番は、多くの企業で採用する標準原価が今の時代には適さないものになってきているためではないかと感じます。
【図1】経営層・現場の不満
標準原価による管理の功罪
多くのメリットがある標準原価ですが、変化の読めないこの時代、そのメリットがむしろデメリットとして顕在化している面が多くあります。
主な標準原価のメリットは、① 速報性、② 管理容易性、③ 簡便性です。
① 速報性とは、実績確定を待たすに原価把握が可能であり「予定値・目標値」として有用であること、② 管理容易性とは、生産量・稼働率によらず一定であり管理しやすい、ということです。
しかし、変種変量で、尚且つ計画変動が当たり前のこの時代、当初予定通りにモノを作ることはほぼできません。
生産量・稼働率等の計画の変化に対して、標準原価では個々の製品に対する影響の実態をタイムリーに表すことはできず、むしろ判断をミスリードすらしかねません。
さらには、標準原価計算で発生する原価差異は多くの企業では工場或いは全社一本でしか把握できておりません。このため最新の実態(すなわち原価差異)を反映した個々の製品原価を補足できず、意思決定を歪めてしまうことも起こり得ます。
③ 簡便性とは、標準原価では計算ロジックが簡易であり、原価計算システム構築時の負荷がさほど高くないことや、緻密な現場情報整備が不要であるという事です。
しかし、原価計算パッケージの大幅な進化により標準機能で対応可能な範囲が大きく広がり、上記はもはやメリットとは言い切れません。
【図2】標準原価の功罪
すなわち、変化の大きい今の時代、標準原価だけでは最新の実態をタイムリーに把握し、様々な判断・意思決定を行うのは不十分であり競争力向上は非常に困難と言えます。
(決して標準原価自体が悪い訳ではなく、標準原価“のみ”では不十分ということです)
“現場に負荷をかけない”製品別実際原価管理
では、標準原価のみでは不十分であるとすると、どのような原価管理が必要となるのかということになります。
そこには、「変動する生産実態をストレートに把握できる原価」、すなわち、「① 製造活動により日々変化する原単位情報」を、「② ダイレクトに製品や工程に紐づけ」、それを「③ タイムリーに把握」した実際原価が必要となります。
【図3】実際原価の要素
この「製品別実際原価」を有用なものとして実現するためには、いかに現場の正確な実績情報を取得できるかが肝となります。
たとえどれだけ素晴らしい原価計算の仕組みがあろうと、正確なインプットなくしては、“garbage in, garbage out(ごみを入れたらごみしか出てこない)”となってしまいます。
今までは、多くの企業において、実際原価の必要性は認識しているものの“正確な実績情報取得”が実現の障壁となっており、実績情報整備において現場を説得しきれず実際原価導入を諦めた(或いは、中途半端な実際原価となってしまった)事例が多く見られます。
しかしながら、工場や現場のIoT・DXの進化により、そのハードルが急速に・大きく低下してきております。
例えば、今まで現場の日報から取得してきた工数情報は、工程監視カメラの画像認識・画像解析により人手をかけずに自動収集できます。また、ARマーカー付き工具とAR認識カメラを用いて、工程別・作業内容別の工数実績の自動取得を行っている工場もあります。
他にも様々ありますが、実際原価把握においてこのDXの進化を活用しない手はありません。
【図4】DX活用事例
一方で、“正確な実績情報取得”のために、いくらでも費用と時間を掛けていいわけではありません。効果と経済性を勘案して収集すべき情報を絞り込むことが重要となりますが特に下記を強く意識する必要があります。
1つ目は、原価管理目的を明確にし、それに従った必要情報を定義することです。
例えば、「経営者目線での意思決定」目的を重視する場合、工程ごとの細かい情報までは必要ありません。
ポイントは、製品別・拠点別・工場別等の経営意思決定に必要な粒度を見極め、いかに早く“お金”というものさしで原価に置き換えて経営層に報告するかということになります。
一方、「生産現場合理化」を目的と置く場合、必要情報は大きく変わります。
日別・工程別の作業員ごとの工数のバラつきや、生産ロット別のロスの傾向、あるいは、生産設備ごとのバラつきといった、個別の作業のバラつきや改善箇所を特定できる情報が必要となります。進んでいる企業では、環境変数として従業員の体調・気候・湿度等の情報と、作業能率やロス発生率を紐づけて相関分析を行っている事例もあります。
2つ目は、実績情報を収集すべき工程を絞り込むことです。
全ての工程の実績情報を取得しても、活かせなければ意味がありません。
例えば、在庫が多く滞留する工程、あるいは、原価が多くかかっている工程、バラつきが大きい工程、不良が多く発生する工程等、現場改善等の具体的なアクションを行うべき工程を絞り込むことが重要です。
逆の言い方をすれば、機械工程で安定的な生産を行えている工程では、予定値をそのまま実績とみなしても問題なく、実績情報取得は不要となります。
3つ目は、今ある情報を活かすことです。
製品別実際原価を目的としたときに、全てのコストを製品別に把握しないといけないわけではありません。
例えば、混合工程で製品別の工数を取得するということは、多くの場合、現場から猛反発を食らいます。ともすると、実際原価構築の取組自体が進まなくなってしまいます。
その場合に重要な観点が、既存のデータを組み合わせて、活動実態を仮定計算によって必要な情報を作成するとこいうことです。
例えば、販売部門が顧客別に営業工数を管理している場合、新たに製品別の工数を記録してもらうことはあまりに難易度が高いため、既存の顧客別工数で営業費用を顧客別に配賦し、その後、販売台数などで製品に配賦するといったやり方です。
このように、精度と難易度のバランスを踏まえ納得感ある妥協点を探ることが重要になります。
これからの時代の原価管理とは
冒頭で申し上げた通り、製造業を取り巻く環境は日々急激に変化しており、誰しも確度高く将来を予測することはできません。
そのような状況下で適切な事業判断を行うためには、変化する内外環境をタイムリーかつ適切に反映した製品別実際原価管理の導入が必要となります。
加えて、企業実態に合わせ適切にDXを活用することでQCDに優れた原価管理の導入が可能であり、競合他社の一歩先をいったコストマネジメントの世界が開けてきます。
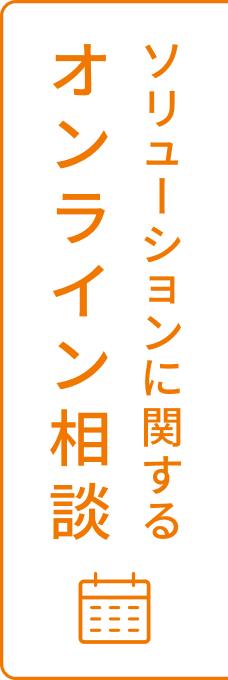
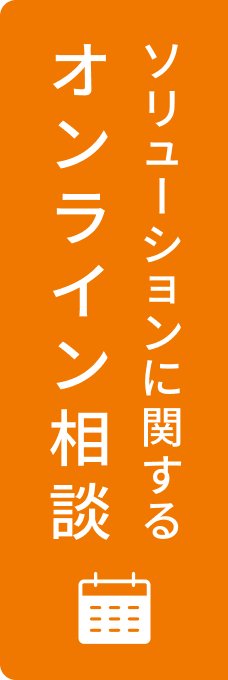
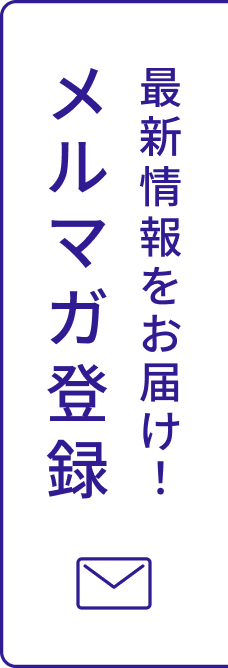
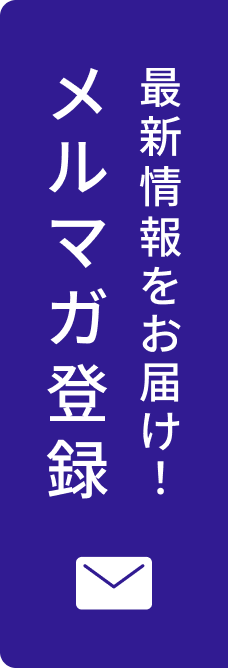
オンライン相談問い合わせる メルマガ登録
最新情報をお届け! メルマガ登録
この記事の執筆者
職種別ソリューション