サプライチェーンの不確実性に立ち向かう
製造現場の高速マネジメント
本稿では、PSI(製・販・在)計画の急激な変動に製造現場が迅速に対応していくための要点について解説いたします。
計画の変動は当たり前 求められる発想の転換
自然災害や地域紛争といった想定していない事象をきっかけに需要や製造・物流環境が一変し、PSI計画にも多大な影響を及ぼすケースが発生してきています。その影響は時に市場が求める機能や製品、需要地やニーズの強さ、物量、生産地や生産ミックスなどの要素までも目まぐるしく変動させます。
もちろん、このような大規模な変動を完全に予測することは不可能です。従って、予測の精度を上げるのではなく、変動を捉えた後にいかに迅速かつ柔軟に対応していくかが今後のポイントとなります。具体的には製造品目の切り替え容易性を確保しつつ、切り替え判断と実行(製品供給)までのリードタイムを短縮化しておくことが重要となります。
では、この切り替えを可能にするためには何が必要なのか、3つの変革ポイントが挙げられます。
【図1】PSI計画が変動する中、サプライチェーンの現場に求められること
変革ポイント① 意外と揃っていない?現場の可視化すべき情報
もし今急激な需要変動によって速やかな生産品目の切り替えが求められた場合、おそらく「できる」と断言できる企業様は多くないでしょう。
従来、日本企業では、如何に同じ品目をまとめて効率的に生産するかを重視する傾向にあり、それに適したものづくりや情報収集が行われてきました。結果として、生産に必要な材料の在庫状況や設備制約、切り替え可能工程といった生産品目の切り替えを判断するための情報が必要なかたちで揃っておらず、判断が難しくなっているものと考えます。以下でもう少し詳しく解説します。
~把握できていない材料在庫~
生産品目を切り替えるにあたって、そもそも必要な材料在庫が本当に揃っているのかが分からなければ製造可否は判断できません。
在庫の可視化には3つの要素があります。
第一に、在庫数量の可視化です。生産品目を切り替えようとすると、製造拠点の理論在庫確認に始まり、サプライヤでの対応可否確認、さらにはグローバルも含めた在庫の移動可否等を検討していくことになります。そのためには、生産品目の切り替えで必要になる材料在庫が、使える場所に、使える状態でいくつあるのか(近く補充予定なのか)時間をかけることなく把握できなくてはなりません。ただ、例えば複数の拠点で同じ品目を取り扱っている場合でも拠点間でのシステムやデータの違いで即時把握がかなわないケースや、積送中や引き当て済みなどの在庫の状態が見えずに結局最終判断を人力で行っているケースが散見されます。まず、在庫情報を共有していくためのデータ整備が重要になります。
次に、材料在庫から見た生産可能品目の可視化です。昨今では特定の材料の供給が遅れたり停止したりするという事態が実際に起こり得ます。「材料がないために製造/出荷できない」という事態は企業活動そのものを停止させてしまう可能性があります。そのため、常日頃から代替可能となる材料を検討・把握しておくことはもちろんですが、既存の材料在庫からどのような製品の供給が可能か、売れる可能性のある取引先と併せて確認できるようにしておく必要があります。材料供給の遅れ・停止が発生したとしても、機会損失を別の品目・取引先への売上で補填していくという逆転の発想が重要です。
【図2】可視化のポイント~材料在庫から見た生産可能品目~
最後に、在庫内訳の可視化です。従来は必要なモノは必要な時に必要な分だけというJITの考え方が基本でしたが、不確実な状況下においては本当に代替のきかない材料やL/Tが長い材料などについては意思をもって戦略的に在庫を積み増すことも必要です。ただし、単純に在庫数を増やすだけでは適切なコントロールはできません。供給リスクに備えるための在庫なのか、価格高騰リスクに備えるための在庫なのかといった目的別に区分管理を行い、例えば「特定のリスクが健在化した場合に復旧まで持ちこたえるための在庫量」といった具体的な見積もりが重要です。
【図3】可視化のポイント~在庫内訳~
~不足している設備制約情報~
既にスケジューリングのために設備制約を情報管理されている企業はあると思います。ただ同時に、メンテナンス負荷が高いこともあり、網羅的にかつタイムリーにデータを最新化できていない企業も多いことでしょう。設備ごとに製造可能な品目の定義や、金型・治具などの使用器具の情報管理、利用回数やメンテナンスを含めた状況管理などの内容を常に管理・維持していくことが生産品目切り替えを素早く判断していくための大前提となります。
~把握できていない切り替え可能工程~
これまで、製造効率や手配効率を考慮し、製造指示単位やラインの構築単位は比較的大きく設定される傾向にありました。生産品目の構造や仕様を考えればより細かく設定できたとしても、効率性を優先してきたのです。しかし、いまは頻繁に作るべき製品が変わる状況です。この変化に追従するためには、複数品目共通の工程と特定品目固有の工程とを切り分け、製造上の切り替え可能なポイントとして明確にすることで効率性を考慮しながら製造指示単位を見直すことが重要です。
【図4】可視化のポイント~切り替え可能工程~
変革ポイント② 目指すのは、ペーパーリードタイムの極小化
生産品目の切り替えを判断するための情報が揃ったとしても、それらを使って完全自動切り替えとはいかず、最終的にはヒトの仕事になります。しかし、現在はその他の業務に時間を取られ、本来ヒトが行うべき業務に十分な工数をかけられていない状況であるように思います。余剰を生み出す方法として、ペーパーリードタイムの極小化が考えられます。
これまでも製造や手配業務について自動化や短縮化に取り組まれてきた企業が多い中、改めて業務効率化の余地として着目いただきたいのは部門や業務、拠点間などの「際(きわ)」です。このような「際」には、いわゆるバケツリレー/人海戦術で情報を連携させるなど本来不必要な業務を強いているケースが多く存在しており、ここにペーパーリードタイムの極小化を図れる余地があります。
一気通貫のデータ連携基盤を構築し、知りたい情報を必要な時に誰でも得ることができる仕組みを整えることで、判断に必要な情報収集・加工などのオペレーション業務に時間をかけるのではなく、ヒトが意思決定業務に集中できるようにすることが重要です。
【図5】部門間に眠るペーパーリードタイムの極小化の余地
変革ポイント③ サプライヤ連携の強化
垂直統合が弱まり、機能分化が進んで一社でモノづくりが完結しなくなった昨今、生産品目を柔軟に変えていくためには、材料手配の面で一緒になって変動に追従してくれるサプライヤとの連携強化が不可欠です。ただ、多くの取引先が存在する中で、連携強化を確実に推進していくためには、リソースを全方位に分散させるのではなく、まずメリハリをつけることが重要です。材料ごとに、自社とサプライヤ、同じ材料を使用する他社との位置付けを明確にしつつ、各サプライヤとの関係性をどのように構築していくのかビジョンを明確にしておく必要があります。その上で、自社製品のコアとなる材料および、自社に甚大な影響がある優先度・重要度の高いサプライヤからは生産能力情報を共有してもらうだけでなく、自社からも顧客からの需要情報やそこから見積もった見込み手配数量を逐次共有するなど、サプライヤにもメリットのある連携体制を敷くことが重要です。
また、さらに重要なのは、このビジョンに基づいた評価と調達活動を継続することです。自社における重要部品やサプライヤとの位置関係は常に変動しますし、例えば計画を密連携していけるようなサプライヤとの戦略的関係は一朝一夕では構築できません。評価を定期的な業務活動に落とし込むとともに、生産・購買に加えてESG/SDGsなど、多くの目的を担う・複数部門を巻き込んだ大きな活動に仕立てていくことが重要です。
【図6】サプライヤ連携でメリハリをつけるための視点
サプライチェーンの不確実性に立ち向かうために
ここまで、頻繁に発生する状況変化にサプライチェーンの現場が追従していくためのポイントを述べてきました。内容をまとめます。
1.生産品目が「変化」することを前提として現場情報を可視化する
‐在庫 ~多方面から在庫情報を捉える~
‐設備制約 ~基礎情報を鮮度よく維持~
‐切り替え可能工程 ~生産指示やライン構成単位をより小さく見直す~
2.ペーパーリードタイムの極小化を目指す
‐部門や業務の「際」にペーパーリードタイム極小化の余地あり
3.サプライヤ連携の強化
‐強化は全方位にではなく選択と集中
‐ビジョンを共有し、会社全体の活動に仕立てる
以上となります。
今回ご紹介した内容の詳細については、是非お問い合わせください。
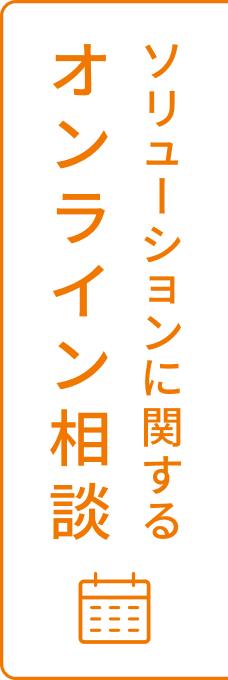
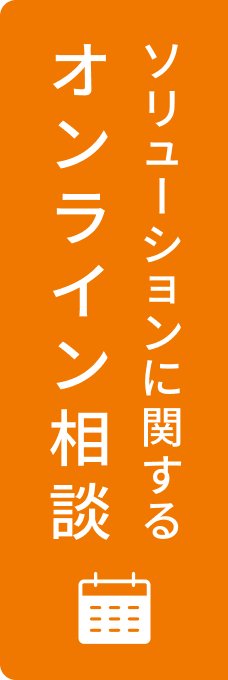
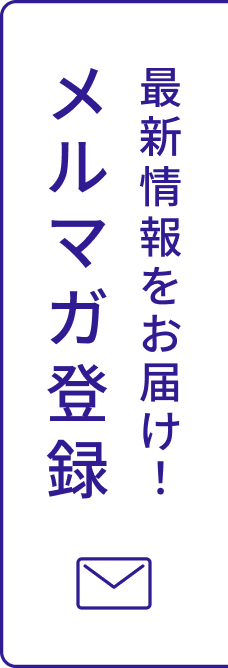
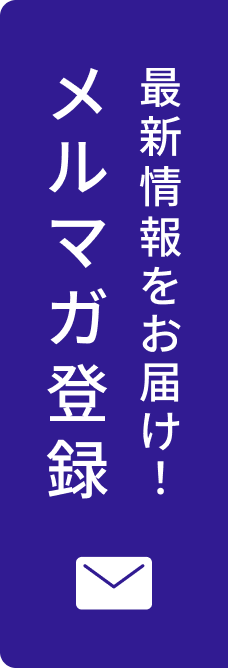
オンライン相談問い合わせる メルマガ登録
最新情報をお届け! メルマガ登録
この記事の執筆者
職種別ソリューション