2025/04/25
在庫管理とは?(後編)~在庫削減の方法と改善事例~
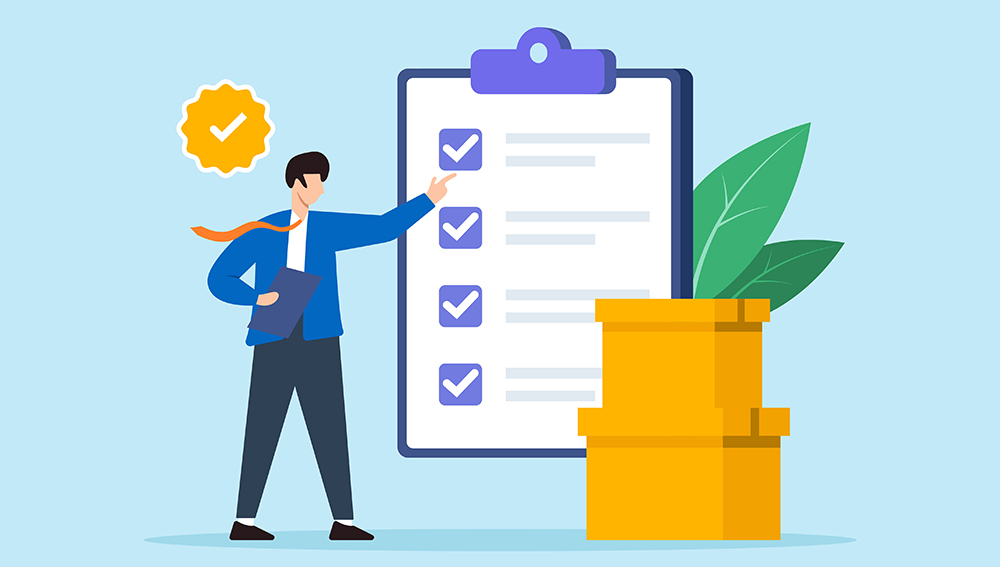
コラムの後編となる本記事では、在庫適正化に向けた削減方法を紹介するとともに、在庫を切り口とした企業改革の事例まで踏み込んで解説します。
※前編はこちらとなります
在庫管理とは?(前編)~基本の解説から見える化の方法~
在庫の削減方法
現在の在庫が適正在庫を超えている場合に、在庫を削減していく具体的な方法を解説します。様々な方法がありますが、超過している原因を分析するなどして、最適な方法を探す必要があります。
不良在庫の処分
不良在庫とは、不動在庫、使用期限切れ在庫など、市場に出せなくなった在庫を指します。これらは在庫回転期間をABC分析することで特定することができます。通常の過剰在庫との違いとして、過剰在庫がまだ売れる見込みがある一方で、不良在庫はこのまま売れる見込みがないものです。不良在庫は無駄な保管コストが増大する原因となるため、以下のような方法により処分が必要です。
-
- 値引き販売
- 廃棄処分
- 業者による買い取り
また不良在庫を処分する際には、併せてなぜ不良在庫となったのか原因を分析して、対策を講じることも必須です。
部材の発注方式の見直し
部材の在庫を削減するためには発注方式を見直すことも重要です。部材の発注方式には、以下の4方式がありますが、一概にどの発注方式がよいといえません。自社の商品ごとに需要の変動性や在庫の流動性などを考慮し、発注方式を決定したうえで定期的に過去実績に基づいて見直しを行うとよいでしょう。
定期・定量発注方式
決まった時期に決まった量の部材を発注する方法です。需要予測や発注量の考慮は行いません。需要がかなり安定している在庫に向いています。発注業務に手間は掛かりませんが、在庫の過不足を定期的にチェックする必要があります。
定期・不定量発注方式
「毎週火曜日」「毎月1日」というように、一定のサイクルで部材を発注する方法です。発注時期が在庫量に影響されないメリットがある分、発注量を都度過去の需要データに基づき算出する必要があるため手間はかかります。しかし、市場のニーズに柔軟に対応でき、欠品が防げるので、高流動品や、需要の変動が大きい在庫、重要度が高い在庫(ABC分析におけるAグループ品目等)に向く発注方法です。
不定期・定量発注方式(発注点方式)
定量発注方式は、事前に決めておいた部材の在庫数が下回ったタイミング(発注点)で、一定の数量だけ発注する方法です。発注量が決まっているため発注の手間が掛からず、人件費を削減できるでしょう。ただし、需要変動に対応しづらいため、安価なもの、低流動品、需要変動が少ない在庫に向く発注方式といわれています。
不定期・不定量発注方式
在庫を持たない受注生産方式の場合などに採用される方式で、受注のタイミングで需要量分の部材だけ発注します。
安全在庫の定期的な見直し
基本的な適正在庫の基準値として、安全在庫+サイクル在庫が使われることは上述の通りですが、その安全在庫の基準を、PDCAを回すなかで引き下げることで、在庫の削減が可能です。
安全在庫の計算式である「安全係数 × 需要量の標準偏差 × √(調達リードタイム+発注間隔)」のうち、安全係数は欠品許容率に応じて決まるため、欠品リスクをどの程度負うかにより上下します。(例:欠品許容率5%であれば安全係数は1.65、10%であれば1.29となる)
ですので、欠品による影響度が少ない場合や、過去の欠品実績から想定より需要量のばらつきが少ない場合は、安全係数を引き下げて在庫量を削減することも可能です。こうした、安全係数の見直しを定期的に行うことにより、過剰在庫を防止することができます。
また、発注間隔を短くするために高頻度に発注することでの見直しも考えられます。例えばコンビニでは多頻度小口納品によって店頭在庫の極小化に成功しています。しかし、頻度が増加することで、輸送や倉庫管理コストが上昇するため、在庫負担とのバランスや優先順位を考える必要があります。
需要予測の精緻化
需要予測とは、販売する商品が現時点の市場において、どの程度需要があるのかを予測することです。発注量を決める際に、年間平均需要量を使用するのではなく、これまでの販売統計データや直近の人々の行動に基づき需要予測を行うことで在庫管理の精緻化を図ることができます。また、近年ではAIによる需要予測の技術も進化しており、需要予測の精度を向上させるためにツールを導入することも一案でしょう。
リードタイムの短縮
製造業において、製造などのリードタイムの短縮も製品や仕掛品の在庫適正化に効果的です。製造にかかる日数が減れば、その日数分の製品や仕掛品の在庫が減るためです。また、製造リードタイムが長ければ、製品の欠品時に顧客を待たせることになり、顧客の要求するリードタイムを上回ってしまうと失注の可能性も生じます。そういった販売機会を逃すリスクを減らしたいために、多くの在庫を抱える悪循環も起こりかねません。
さらに、顧客に製品を届けるまでのサプライチェーン全体を見渡すと、製造リードタイム以外のリードタイムが存在します。以下にサプライチェーンにおける各リードタイムと短縮方法を説明します。
【図1】リードタイムの種類
① 調達リードタイム:原材料や部品の発注から自社に納入されるまで
【短縮方法の例】
-
-
- 生産地近くでの現地調達すること(特に海外)
- VMI(Vendor Managed Inventory)として自社工場の近くにベンダー所有の倉庫を持つ
-
② 製造リードタイム:自社で原材料等から製品が出来るまで
【短縮方法の例】
-
-
- 生産方式の見直し(完全受注生産⇒受注組立生産等)
- 製造工程の改善(設備導入による工程の短縮や、品質改善による不良発生率の低減等)
-
③ 物流リードタイム:出来上がった製品が顧客に届くまで
【短縮方法の例】
-
-
- 出荷業務プロセス(ピッキング・検品・梱包等)の見直し
- 輸送手段や配送業者の比較検討による見直し(トラックからフェリー等)
-
④ 顧客納入リードタイム:顧客の発注から製品が顧客に届くまで
在庫形態の見直し
調達・製造・物流の各リードタイム短縮は限界が来ているという場合もあるでしょう。しかし、在庫形態として、原材料・部品・仕掛品・完成品のどの形態で在庫を持つかを見直すことにより、各リードタイムが短縮できなくてもトータルの在庫を削減できることがあります。
顧客の立場としては、上述の顧客納入リードタイムのみが重要であり、顧客からの要求リードタイムに対して、顧客納入リードタイムが下回るようにする必要があります。とはいえ、全ての顧客に対して完成品在庫を持ち受注後即日出荷しなければならないといった極端なケースは考えづらいでしょう。サプライチェーンの下流において完成品として多くの在庫を持てば、その分、加工費や経費も上乗せされた在庫金額となってしまいます。そのため、顧客の要求リードタイムを満たしつつも、よりサプライチェーンの上流において仕掛品や原材料の形態で在庫を保持することで在庫金額を抑えることができます。また、設計においてモジュール化や部品共通化が出来ていれば、1種類の材料や部品を複数の製品に使うことが出来るため、汎用性の高い状態で在庫を持つことで、在庫の流動性を高めると同時に、生産計画の見直しにも柔軟に対応可能となる効果もあります。
業界ごとによって顧客の要求するリードタイムの傾向は変わりますが、顧客からの要求リードタイムに対して、顧客納入リードタイムが下回るようにしつつも、なるべくサプライチェーンの上流で在庫を持つことが理想的です。
在庫管理の改善事例
ここからは、当社の製造業でのクライアントでの在庫管理の改善事例を2つ紹介します。
Case1:生産方式の見直しを伴う在庫削減
- クライアントは、多品種の製品を国内外にある複数の販社を経由し販売しましたが、保有する在庫の増加に悩まされていました。その原因を探ると、大きく2つの課題を抱えていることが分かりました。
-
- 機種別・販社別の適正在庫量が分からないため、過剰な在庫を持っている
- 各製品の生産方式まで踏み込んだ改革が出来ていない
(完全受注生産/受注組立生産/見込生産が混在)
- そのため、以下3STEPのアプローチをとることで生産方式の変更まで踏み込んだ改革を実現することができました。
-
- 生産方式の見直し候補となる機種×販社を抽出し在庫を分析
- 在庫削減余地のシミュレーションによる打ち手を検討
- 販社別・機種別の四半期末在庫目標を設定し、PDCAを回す
【図2】生産方式の見直しを伴う在庫削減の事例
Case2:CCC短縮に向けた在庫削減
- こちらはCCC削減を目指すクライアントの事例です。在庫回転日数の短縮のために手を打ちたいものの、在庫削減のターゲットが見えず、また、在庫増加の原因も見えていないという状況でした。
- そのため、以下3STEPのアプローチを取ることで、在庫回転日数を短縮・CCCの削減を実現できました。
-
- 在庫分析によりターゲット品目を絞り込む
- ターゲット品目のサプライチェーン上の在庫管理点ごとに詳細な分析・真因抽出を実施
- 短期・中期の打ち手を立案・実行
【図3】CCC短縮に向けた在庫削減
まとめ
前編・後編の2回に渡り、在庫管理の基本から手法、改善事例までを解説してきました。
製造業における在庫管理とは、経営やサプライチェーン全体と関わる重要な要素であり、在庫を適正化することでキャッシュフロー・利益の改善を図ることができます。
また、当社レイヤーズ・コンサルティングでは、これまでクライアントの在庫の分析を切り口としてサプライチェーンの改革に繋げるようなご支援を実施してきました。もし、在庫管理やサプライチェーンについての課題・お困りごとがあればレイヤーズ・コンサルティングにご相談いただければと思います。
在庫管理に関する当社最新ソリューションは、こちらからご覧いただけます。
在庫は悪か?~VUCA時代の在庫戦略~
PSI計画の変革でサプライチェーン強化~トランプ関税を乗り切り、儲かるSCMへ~