BOP(Bill of Process)とは
~グローバル最適生産を実現する新トレンド~
そのような中、コロナ禍、半導体不足、欧米中露摩擦など予期せぬ変化でサプライチェーンはさらに混乱しており、変化に強い柔軟なものづくりが求められています。
これらの環境変化に対応しながらグローバルでの最適生産を実現するためのシステム機能として今、BOP(Bill of Process)が注目されています。「BOP」とは何か。具体例を交えてご紹介いたします。
今、なぜグローバル最適生産が求められているのか
製造業では日々変化する需要変動、地震・豪雨など自然災害、欧米中露摩擦、それらに伴うサプライチェーンの断絶、労働人口減少に対応した生産性向上など、製造現場は柔軟なものづくりが求められています。
日々、突発的な環境変化に対応するためには、グローバルでいつでも、どこでも同じ製品を作れる状態をつくり、有事のリスクを最小限に抑えることが重要です。
柔軟なものづくりを実現するためには、工程情報の標準化が重要となりますが、現状多くの製造業では工程情報を各拠点で個別管理しており、標準化/可視化もされていないことがあります。
そのような中で、PLM(Product Lifecycle Management)システムの新機能であるBOPを導入し、製品開発を行いながら、各生産拠点の設備、リソース情報を共有・可能な限りグローバルで生産工程を標準化し、これをPLMで一元管理して各拠点に展開する企業が増えています。
【図1】拠点毎の工程情報管理の実情
BOP(Bill of Process)とは
BOPとは、Bill of Processの略称で、日本語では製造工程表と呼ばれます。
生産工程の工程順序、設備、作業内容、工程品質などの単位を設定し、生産準備情報を登録してMES※1と連携します。
BOPとよく似たものにBOM(Bill of Material)があり、主には設計BOM(Engineering-BOM以降E-BOM)と生産BOM(Manufacturing-BOM以降M-BOM)があります。
E-BOMは設計部門が作成する部品表で、製品を構成する全部品を設計単位に体系化して管理します。
M-BOMは製造部門が作成する部品表で、E-BOMを基に製造に必要な部品、資材、購買情報を製造単位に体系化して管理し、ERP※2へ連携します。
一般的にM-BOMは生産拠点によって工程や購買情報が異なるため、拠点毎に作成し管理されます。
また、M-BOMには工程情報を持っていないことが多く、持っていても一部の工程情報のみであることが多いのが実情です。
BOPは生産に必要な工程情報をグローバルで網羅的に管理し、生産に関わる情報の一元管理を可能とします。
※1 Manufacturing Execution System:製造実行システム
※2 Enterprise Resource Planning:企業資源計画
【図2】E-BOM、M-BOM、BOPの定義
BOPの活用と効果
【フレキシブル生産】
BOPにグローバル各拠点の工程情報が登録され一元管理することで、有事の際、フレキシブルに生産拠点を変更し、生産活動を維持・継続することができます。
【設計・生産・製造を橋渡しする共通言語】
すべての拠点で共通の管理項目で工程を表現し、設備・治具、品質、作業指示、設備メンテナンス履歴や、作業者教育実績などの情報をBOPに蓄積し、他の生産拠点や関連部門に公開することで暗黙知だった情報を形式知化することができます。
【品質トレーサビリティ強化】
工程情報、BOM、生産拠点情報が統合管理されていない場合、不具合発生時の影響調査をするためには各工場への問い合わせが必要となり、膨大な手間と時間が必要となります。
BOPとBOMを関連づけて統合管理することで、設計変更や不具合が発生した際に、部品だけでなく工程や設備も含めた影響範囲の特定が可能となり、グローバルで迅速に対処することができます。
【開発上流でのコスト作りこみ】
開発の上流段階での原価作り込み・コストダウンの検討を行うためには、BOMだけでは、材料費の積み上げしかできません。BOPに各工程における加工費の原価情報を持たせることで、実績ベースの製造原価を含めたコストシミュレーションが可能となります。
【図3】BOPによる品質トレーサビリティのイメージ
BOP導入時には製造工程の標準化とコンカレントエンジニアリングも重要
BOPはE-BOMと同じPLMシステム上で管理することにより、データ連携も可能となります。よって、新製品のBOPの作りこみはE-BOM作成と並行しながら、コンカレントにグローバルの生産要件を織り込むことが重要です。
またBOPは、マザー工場で製造することを前提として作成します。その後、生産拠点ごとに異なる部分を変更して各生産拠点に配信します。
この時、生産拠点ごとに異なる部分を最小化するために、全生産拠点の製造工程を可能な限り標準化することが重要となります。
コンカレントエンジニアリングにより新製品を短期間で立ち上げることが可能となり、BOPをPLM上で統合管理することで、世界同時立ち上げやグローバル生産拠点全体で一貫したものづくり品質を維持することができます。
また、需要変動に応じた最適地生産の検討や、不測の事態の際には、代替生産可能な工場を迅速に把握し、柔軟な生産移管を行うことで、チャンスを逃さず事業継続することができます。
【図4】コンカレントエンジニアリングとBOPの一元管理
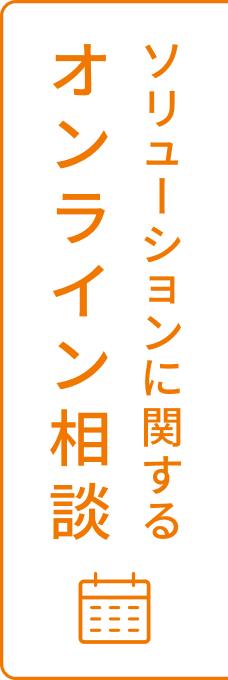
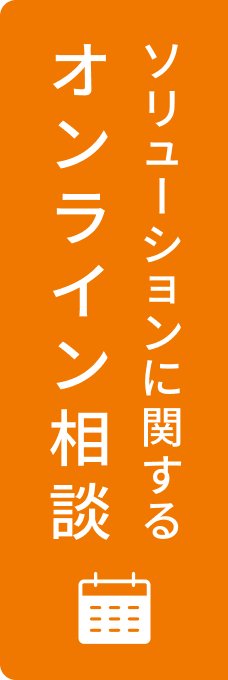
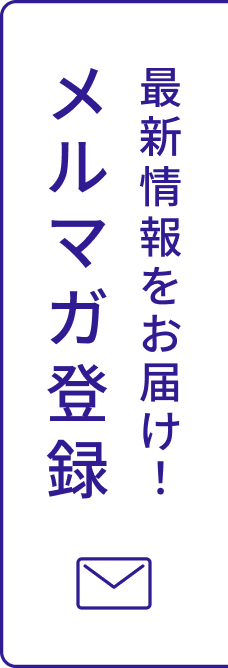
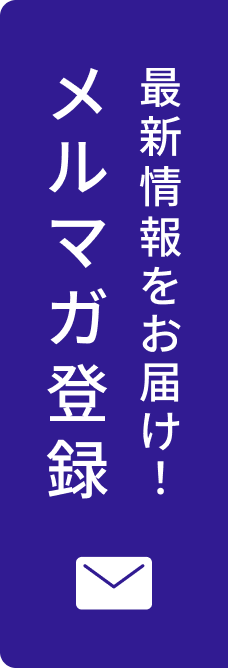
オンライン相談問い合わせる メルマガ登録
最新情報をお届け! メルマガ登録
この記事の執筆者
職種別ソリューション