【コンサル視点の原価管理】
②成果が出ない原価の視える化
原価計算/原価管理とは何を目的に行うのでしょうか。
自社の原価情報が見えないことに課題意識を持つ企業では、明確な目的を定める前にまずは視える化から始めようと試みるケースも多いかと思います。
しかし、実際に活動を始めてみようとすると、活動を推進したい経営層⇔負担の重さを理由に反発する現場の間で温度差があり、経営層が思うような活動が推進しないケースも多く耳にします。
本稿では、
ー経営層⇔現場間の意識のGapは、現場が活動内容に納得していない事が原因であること
ー「まず実態把握から」の思想が、原価情報へ必要以上の精度を求める結果を招くこと
ー原価情報が見えるようになることへの不明瞭な期待から、取り組み開始時点で十分な活用ニーズの掘り起こしが行われないこと
これらの内容を、背景に触れながら深掘りしていきます。
経営層⇔現場間の意識のGapは、現場の納得が得られないことで起こる
原価情報に対する課題意識が高まり、視える化を推進する取り組みが始まるきっかけの多くは、経営層が打ち出す方針にあります。経営方針上の重点的な取り組み事項として「原価管理の強化」などが掲げられ、経営トップから指示を受けた原価計算の担当部署(経理部、原価企画担当部署など)が活動を推進するケースです。当社が支援を行ってきた企業では、こういった経営トップが掲げた取り組みが思いどおりに推進しない状況が多く見受けられます。これはなぜなのでしょうか。
理由の一つに、経営層⇔現場間での原価情報に対する温度差が挙げられます。
経営層は、各事業セグメント/製品が達成すべき利益目標に資する利益を創出できているかどうか、原価(金額情報)をもとに判断を下すことでアクションに繋げる役割を担っています。
一方で現場(本稿では製造業でのモノの加工・組立を指します)は、品質(Q)/コスト(C)/納期(D)が基準を満たすかどうか評価し、日々の原価低減活動を通じて改善を図る役割を担いますが、それらの評価を金額ベースとして行うことはなかなかありません。
具体的には、
ー製造指図ごとに、標準時間以内に作業ができているかどうか(時間の評価)
ー加工/組立不良の発生数量がどれだけであるか(不良数・不良率の評価)
など、大半は製造にかかわる管理指標で改善活動を評価しているのです。
現場にとって原価低減活動の主眼は「改善」であり、製造にかかわる管理指標が改善できていれば良いという考え(=その結果が金額ベースでどれだけ改善できたかまでは見ない)が念頭にあることも、原価情報を指標として意思決定を行う経営層とのGapを助長する要素となっているのです。
「まずは実態把握から」が招く、原価情報の精度偏重
「原価管理の強化」を掲げて取り組みを推進しようとする経営層も、実は原価管理を強化できている状態を漠然と捉えており、明確な状態目標をイメージしない中で活動を指示することも少なくありません。
ゴールイメージが漠然とした状態であっても、掲げた指針に基づく活動を進めることになり、ここに本来の活動目的と取り組み内容とのGapが生じることになります。原価管理に対する解像度が低い中でフォーカスされがちなことは、「まずは実態把握から始めよう」とする動きです。
前述のとおり、経営層は各事業セグメント/製品の利益および原価を金額ベースで評価することになります。これらの評価に活用する金額が実態から遠ざかっていると判断を見誤りかねないという意識から、実態を表した金額を求めるようになります。
最たる例が、生産活動の各断面に対する実績収集です。
自社内で加工・組立を行うメーカーを例に取ると、往々にして以下のように必要以上の精度を追求した実績収集を現場に強いることとなります。
◆従業員の稼働状況(ヒト)
加工・組立作業に対して掛かった「実際の」時間を漏れなく記録しようとする
さらに、加工の正味時間/段取りの時間/その他の時間も区分記録をしようとする
◆物品の購入/生産/販売による増減や移動(モノ)
倉庫だけでなく、工程間の細かな滞留在庫に至るまで正確な位置を特定し、その単位で在庫を集計しようとする
◆加工・組立に掛かる諸費用(カネ)
製造部門別だけでなく、考えうる現場の最小活動単位(作業ライン別、手順別など)まで落とし込んだ発生費用を集計しようとする(社員区分:正社員/契約/派遣ごとの労務費や、治具/工具/消耗品/光熱費に至る明細ごとの経費など)
◆諸費用の賦課基準(計算ロジック)
水道光熱費を、厳密なメーター記録による実際使用量をもとに賦課しようとする
経営層にとっては、これらの実績収集の結果として実態把握に資する原価情報を取得できることになるかもしれません。一方で、従来の改善活動を金額ベースで評価してこなかった現場にとっては、実績収集は負荷が高く、彼らに対するリターン(ご利益)も少ないと感じられることから、当然ながら活動に対する反発も出ることとなります。
【図1】原価管理を強化するために、精度を追求した実績収集を行いがち
注力すべきポイントが決まらず、原価情報に濃淡がなくなる
前段でご紹介したような要素全てに対して精度を高く情報取得を試みると、大変な手間と時間が掛かります。それだけでなく、実態把握を念頭にした原価情報であることを追い求めた結果、「特に注力して管理すべき費用」と、「それほど注力の必要がない費用」の濃淡が付かなくなってしまいます。
ここで本来の原価管理目的に即して考えると、企業全体に占める金額インパクトが小さく、かつ日々の発生状況の変動がそれほど大きくない費用であれば、実態に即した発生額を緻密に記録する意義は低いでしょう。また、前段でも示してきた経営層⇔現場(例えば、ある作業ラインのリーダー)それぞれの立場で必要な情報を考えてみれば、粒度/鮮度/精度はもちろん異なるはずでしょう。
ひとえに原価情報と言っても活用目的・立場によって必要な情報に濃淡はあるはずですが、全ての情報に対して精度の高い情報を求めると、必ずしも精度が重要でない費用に対してまで同じ水準を求める結果となってしまいます。
活用目的が明確になりづらいワケ
これまでお話ししたような「視える化」が目的化に陥ってしまう背景には、原価情報の活用ニーズの掘り起こしが行われないまま活動が進んでしまうことにあるものと考えます。
本来であれば、取り組み開始時点で活動目的に立ち返り、ニーズを明らかにした上で取り組みを開始するのが理想的な姿です。
しかし、「実態に即した原価情報」に対する意識が先行してしまうことで、活用目的の検討が先送りされることになります。そればかりか、「原価が見えるようになれば自ずと活用もできるようになる(逆に、見えなければ活用ができない)」という思考に陥ってしまうのです。
加えて、現場により近い立場であるほど、金額ベースではなく時間や不良数・不良率などが指標となっていることも、原価情報へのニーズがなかなか挙がらない原因なのではないでしょうか。
まとめ
当社では、原価計算・原価管理に対する課題の棚卸や、原価管理の目的明確化に向けた支援を多数行っております。「自社内で原価計算の見直しに取り組もうとしているが、活動がうまく進まない」 等のお悩みはもちろん、原価企画/原価管理のソリューションにご興味がある方も、是非お気軽にお問い合わせください。活用目的を定めることで、原価計算・原価管理の仕組み導入に対する活動の濃淡を付けることができ、負荷軽減を実現した事例もございます。
今後の配信では、原価計算に活用目的を持たせる際の難しさや、本来目指すべき視える化(=明確な管理目的を持って原価情報を参照すること)の達成に向けた推進のヒントを中心にお話しします。
【今回の記事のまとめ】
- 原価情報をもとに意思決定をしたい経営層⇔日々の改善活動を金額ベースで評価する機会のない現場の間にGapが生じる
- 原価管理の強化に対する解像度が低く、結果として原価情報に対する精度の高さに偏重した取り組みとなってしまう
- 精度の高い原価計算を行おうとすると、ヒト、モノ、カネ、計算ロジックのそれぞれで極端に子細な情報取得が必要であり、それには大きな負荷がかかる
- 実態把握が主眼に置かれることで活用目的・ニーズの深掘りがされず、結果として原価情報の把握が活用にも繋がる、という思考になる
関連サービス
#サプライチェーンマネジメント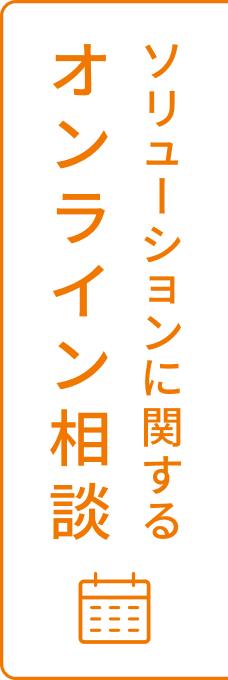
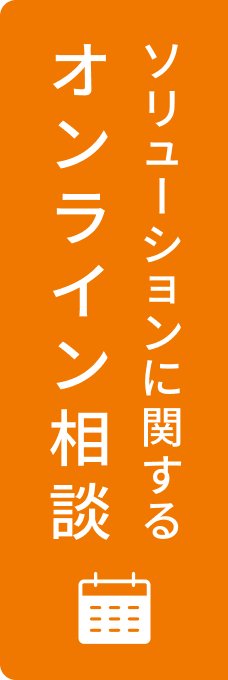
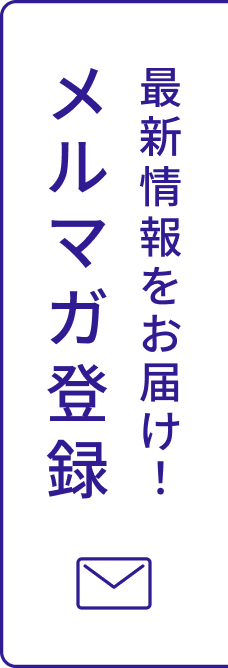
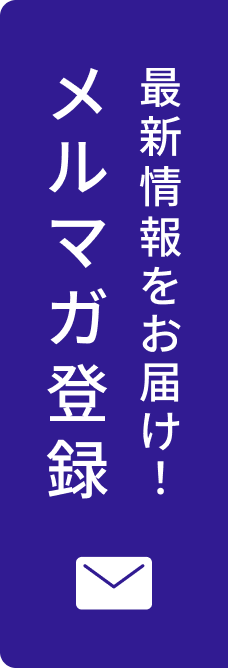
オンライン相談問い合わせる メルマガ登録
最新情報をお届け! メルマガ登録
この記事の執筆者
-
小林 真SCM事業部
マネージャー
職種別ソリューション