2025/02/20
調達部門の未来を切り拓け!環境変化を乗り越える改革アプローチ
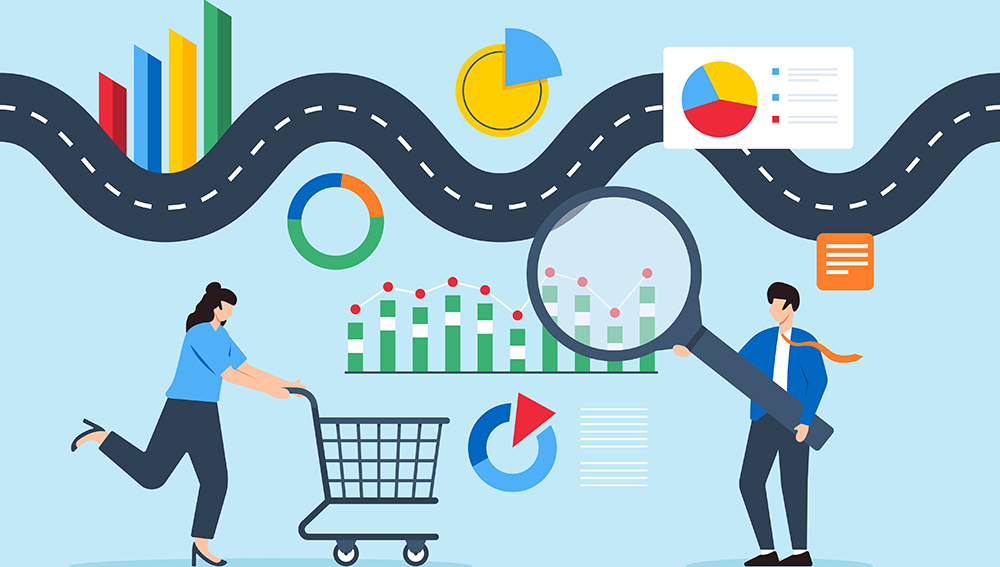
調達部門を取り巻く環境変化とは
昨今、原材料費・人件費高騰や為替変動による調達コストの上昇、地政学リスクや災害によるサプライチェーンの混乱や寸断、 SDGs/ESG環境要求拡大への対応が求められるなど、調達業務の難易度が上がっていると言えます。
2024年の経済産業省の報告によると「原材料費高騰への対応」、「調達や供給網の寸断リスクへの対応」、「環境に配慮した工場操業」といった課題が製造業の抱える上位課題として挙げられています。
(出典:製造業を巡る現状と課題 今後の政策の方向性)
このように製造業を取り巻く環境の変化に合わせて、ものづくりの屋台骨を支える調達部門として乗り越えるべき課題がいくつも出てきています。
調達部門が乗り越えるべき課題
具体的に調達部門が乗り越えるべき課題としてどのようなものがあるか、以下の5点について解説します。
課題①サプライチェーンの混乱・寸断
サプライチェーンが影響を受ける代表的なリスクとして、政治的不安に伴う地政学リスク、自然災害やパンデミックに伴う環境リスクがあり、どちらも発生するタイミング、顕在化する確率の予測が難しいという特徴があります。万が一、サプライチェーンが寸断した場合には、顧客に対する製品・部品供給に関するリードタイムの延長、代替手段での輸送に伴う輸送品質低下といった問題が挙げられます。
あるいは、基幹となる部品を他社に依存していた場合、自社だけの問題では解決し得ないため、復旧までの対応に時間を要してしまいます。突発的なサプライチェーンの混乱や寸断が起きてしまった際には、あらかじめどのような問題が生じるのか、その影響範囲はどこまで及ぶのか想定したうえで、事前に対策することが必要になります。
課題②SDGs/ESGへの対応
依然として、サプライチェーンに関する人権問題、環境問題の関心は高く、いつどのタイミングで問題が表面化されるのか分かりません。一度表面化した場合、問題のあった生産拠点での生産停止や、取引先との取引停止が起こるなど、サプライチェーンへの影響は重大です。問題が起きた後でも、迅速に行動がとれるよう、あらかじめ、どういった部材、取引先が対象となりうるのか、Tier1だけでなく、Tier2以降のメーカー名や製造拠点等の情報を管理しておくことが必要です。
課題③サプライヤーとのデータ連携に伴う高負荷業務
調達業務では、サプライヤーに対する見積りの依頼、生産能力や在庫の問い合わせはもちろん、発注、検収、支払といった多様な業務が、サプライヤーごと(場合によっては製品ごとにルールが異なる場合も)に複雑な業務が存在しています。単なる問い合わせであっても、必要な情報を得るためにシステムを駆使して調査を実施したり、紙面やエクセルと突合させて、ようやく問い合わせの準備が整ったかと思えば、サプライヤーに対する依頼はFAXや電話、メールなど様々な形態で行われており、そういった準備や調整業務に大きな時間を取られています。
課題④調達業務の属人化
課題③につづき、調達業務の種類は多岐に渡ることに加えて、サプライヤーごと、製品ごとに考慮すべき違い(契約時のお作法、必要書類等)があること、定期・不定期な取引先が混在するため、業務のマニュアル化やシステムへの入力が追いついておらず、担当者任せとなる企業もあります。そのような状況の中で突発的な担当者の異動が発生した場合、業務の引き継ぎが十分に行えない場合があります。何より今現在、進行中の業務に関して、どこまで話が進捗しているのか、どのようなことが決まったのかが分からない、といった問題が生じます。業務を円滑に進めるためには、調達に関するコミュニケーションの経緯を記録することが必要になります。
課題⑤調達コストの上昇に伴う原価率の悪化
エネルギー価格の高止まり、円安による輸入コストの増加といった理由で原材料の調達コストは増加傾向にあります。東京商工リサーチの「価格転嫁に関するアンケート」調査によると、本業に係るコストが前年より上昇した企業は73.6%(調査対象会数数2,857社中2,105社)。一方、コスト上昇分を「価格転嫁できていない」は、「原材料や燃料費、電気代の高騰」を挙げた企業の37.9%を占めており約4割の企業が原材料高騰分ですら価格転嫁できていないことが分かります。
(出典:「価格転嫁に関するアンケート」調査 東京商工リサーチ調べ)
課題を乗り越えるための改革アプローチ
それでは、上述した調達部門が乗り越えるべき課題に対して、それぞれどのような改革アプローチがあるのか解説します。
課題①に対する改革アプローチ/サプライヤー重層構造の可視化
サプライチェーンの混乱や寸断を迅速に乗り越えるためにはDXを活用し、あらかじめサプライチェーン全体の情報を可視化しておくことが重要です。
可視化のために有効なのが、サプライヤーからの情報を部材に紐づけた上で、Tier2以降(TierN)の部材情報までを管理範囲に含めるというBOS(Bill of Supplier)の整備です。
BOSを整備しておくことで、有事の際には直接影響のあった部材から、その部材に紐づくTier2以降の部材までを迅速に特定できることで、サプライヤーの切替や代替品の発注といった打ち手に早く取り掛かることができます。
課題②に対する改革アプローチ/SDGs/ESGに関する情報管理
環境問題、人権問題であっても、あらかじめどういった部材、取引先が対象となりうるのか、Tier2以降の情報を管理しておくことが必要です。
例えば、CO2であればBOMの管理項目に、購入素材や加工委託品に関する「CO2排出基準」を保持することで、製品品番別の炭素排出量を求めることができます。
また、人権問題であれば、人権リスクのある特定の地域、素材などの情報を保持しておくことで、部材別ではなく、リスクのある地域や素材を軸として影響範囲を調べることができます。
これらについても、課題①で言及した、BOS(Bill of Supplier)を整備しておくことで、有事の際にTier2以降の部材までを迅速に特定できると考えています。
課題③に対する改革アプローチ/サプライヤーポータルの導入
自社とサプライヤー、拠点と部門といった間での問い合わせやデータの参照業務にかかる時間を減らすために、サプライチェーンで発生しているデータをタイムリーに共有しておくことが重要です。
例えば、DXを活用したサプライヤーポータルの導入が考えられます。ポイントは、サプライヤーの契約状況(会社情報、契約情報等)といった外側の情報だけではなく、内側の情報(在庫、生産能力、生産進捗等)についてもリアルタイムで共有することです。
内側の情報についても共有することで、サプライチェーン全体での在庫削減の取り組みや、生産能力に応じた発注、それに伴う調達の納期の調整スピードを早めることができます。
ただし、資本関係のないサプライヤーがOEMメーカーから、内部情報を提供してもらうことは、なかなか難しいことです。手始めに、こちらから情報を提供した上で、情報共有のメリットを感じてもらうことが必要になると考えています。
メーカーとサプライヤー双方で、情報を共有するサプライヤーポータルを構築することで、自社だけでの努力では実現できないメリットを享受できると考えています。
課題④に対する改革アプローチ/調達版電子カルテによる属人化の阻止
調達業務の属人化や、業務引き継ぎ時の混乱(言った・言わない等)による不利益を避けるためには、調達に関わるコミュニケーションの記録が重要になります。
DXを活用して、調達業務に関する電子カルテ(取引先や品番別にカルテを作成)を構築し、サプライヤーとのコミュニケーションを記録することが有効です。調達版電子カルテにより、医療機関のカルテと同様に過去の経緯も含めて誰がどんな約束をして、どういった対応を行い、どこまで進捗しているのか、これまで担当者に聞かないと分からなかったことが可視化できます。
より発展的になるとAIやチャットBOTを活用し、蓄積した調達版電子カルテの情報の中から、必要な情報のみを瞬時に探すことができると考えています。
課題⑤に対する改革アプローチ/コスト試算ツールの構築
DXを活用したコスト試算ツールを整備し、特に製造初期段階においてコストダウン活動の影響を「その場で」「簡易に」把握できるようにすることで、製造とコストダウン施策検討の同時進行を促進する仕組みを構築しておくことが、コストダウンに役立ちます。
例えば、試算ツールにAIを活用し、パラメーター(仕入数、材料費など)を変えた場合の見積原価との差額を確認できるようにしておくことで、サプライヤーとの金額交渉の参考とすることや、企画時の原価とのギャップを早期に把握することができます。
また、コスト試算ツールをクラウドベースのプラットフォームに構築することで、関係者がリアルタイムでデータにアクセスし、共同で分析を行うことが可能となります。
調達部門から他領域に関与するアプローチ
最後に上記の改革アプローチとは別に、調達部門の活動を設計など他領域にも広げることで、コスト削減に寄与できるアプローチを紹介します。
設計領域への関与
設計段階でコストと品質の8割は決まるという話はご存じの方が多いでしょう。設計や試作が完了し製造工程が見えてきた段階では、調達部門としてどこから何を仕入れるかといった選択肢は少なくなり、調達コストの削減は難しい状況です。一方で、設計段階から調達部門が参画することで、市販品の採用や部品の共通化といった助言ができるため、調達コストを削減できる可能性が高まります。
生産戦略への関与
EMS(製造受託)企業の台頭や、地政学リスクを踏まえた生産拠点の見直しにより、どこで何を製造するのかといった生産戦略を見直す企業もあります。その際、調達部門としては生産戦略に応じた調達戦略の検討(仮に生産拠点を移した場合に、当該地域にどういったサプライヤーがあるか。そのサプライヤーからは安定的に供給可能か等)を行い、経営層や生産部門に情報を提供することで、より良い生産戦略の検討に寄与できる可能性があります。
調達部門のDX改革に対するレイヤーズの強み
現状課題を前提としたままのDX改革の検討や、特定のソリューション・ツールの導入ありきの検討では、調達部門のDX改革は難しいでしょう。DX改革の実現に向けては、やはり目標やありたい姿をサプライチェーン全体で設定し、そのギャップを明確にしたうえで、課題抽出/解決策検討/実行計画策定を行うことが必要です。
特定のソリューション・ツールに頼らないレイヤーズだからこそ、中立的な立場でシステムの目利きができるため、調達部門が直面している課題と真摯に向き合い、解決に導くことができます。
レイヤーズでは、業務視点で実現性を検証(貴社の強みを活かした“Fit to Standard”を模索)できること、これまでの“システム導入の知見”からシステム全体の繋がりを踏まえた適切な要件コントロールを実現できます。
調達DXに関する事例の詳細にご興味のある方は、是非お問い合わせください。