~予算は言ってしまえば仮説~
短サイクル先読み経営の勧め
このような状況下で1年・半年先固定の経営管理体制で十分でしょうか。
先行き不透明な現況下においては、変化する環境に合わせて短サイクルで見通し・計画・施策を柔軟に変更し続ける必要があります。
しかしながら多くの企業ではそれを実現できていない現状が散見されます。
・計画策定の大半が手作業(所謂エクセルバケツリレー)で計画づくりに多大な時間・リードタイムを要する。
・外部環境変化が大きい場合に、元々の計画前提から検証・見直しが必要となり、1から作るため多大な時間・リードタイムを要する。
・計画上の施策・改善アイテムの計画実績評価ができない。結果改善が進まず、計画上の施策・改善アイテムも「言いっぱなし」で形骸化する。
・実際損益・原価がザックリしかわからないため、計画もザックリ。結果計画と実績の乖離が非常に大きい。
今回は、従来の固定的・硬直的な予算管理ではなく、環境変化に合わせた機動的な予算管理のポイントをご紹介します。
計画策定のDX化・リードタイム短縮
計画策定は所謂エクセルバケツリレーの代表格です。
例えば販売計画を作るだけでもトップ目標・営業企画部門での割付、営業所の積上、差分の差異割付などに労力をかけています。さらにブランド等の商品系部門がはいってくるとより複雑化して、「今、何が最新でどこまで終わっているのか」もわからなくなり、メール・集計ミス・確認・指摘修正作業も膨大になり、結果計画策定リードタイムは長大なものとなりがちです。ただ、昨今では計画策定システムの発達によりシステム上での管理を行い、2度手間等の作業効率化と進捗の見える化が実現している企業もあります。
また、エクセルバケツリレーでの弊害として計画粒度の限界が挙げられます。実際損益・原価を品目の粒度で行っていたとしても、計画粒度がグロスの場合は予実分析もグロスとなります。意味のある予実分析を行うのであれば予算粒度は原則品目の粒度であるべきです。
では(ある程度のシステム化サポートはされる前提だとしても)品目別の計画を全て考えきることができるでしょうか?量産品を前提とした会社でも販売品目・購買品目が膨大なのであれば、全ては難しいでしょうし、個別受注生産型の企業ではより「来年なんの受注がくるかなんてわからんよ」状態であることをよく耳にします。
そこでの対処方法としては、入力値は製品グロスとしておいて、品目に前年比等のロジックで分割しておく方法や、モデル品目で計画を立案する方法があります。
計画値をロジックで品目に分解することで予実分析を意味のあるものとするとともに、販売計画→生産計画→資源計画→原価損益計画を連動されシステム自動計算の幅を増やすことで計画策定リードタイムの短縮にもつながります。また、その自動化により短サイクルでの計画見直しにも寄与します。
【図1】計画エクセルバケツリレーからの脱却
複数シナリオプランニングによる計画変更の迅速化
予算は一般的に1年分の計画をたてます。また、その計画には外部環境の計画前提(以下シナリオ)があり、それを前提として計画を立案します。そして計画前提は1つのケースが大半です。
では外部環境は1年間不変でしょうか。
先行き不透明な環境においては、計画時に複数のシナリオを置き、シミュレーションを繰り返しながら計画を立案することが有効だと言えます。
まず、計画段階では複数のシナリオに対するシミュレーション結果を検討することで、とるべき戦略と改善施策の議論が活発になり、より具体的な計画づくりに役立ちます。
最終的には1つのシナリオを前提とした計画とはなりますが、多のシナリオでのシミュレーション結果も保存しておきます。
実行段階に現実とシナリオの乖離が大きくなった場合には、別のシナリオに変更した着地見込みを作成することで計画再作成のリードタイムを圧縮することが可能となります。
【図2】複数シナリオプランニング
施策・改善アイテムと予実差異の連動による施策実行・改善推進の促進
多くの企業において予算作成時には施策・改善アイテムを検討して結果を予算に入れ込みます。ですが「作っただけで検証もしていない」、「各部門独立してやっていて会計・予算情報と整合しない」、「予実差異と改善アイテムの差異の合計があわない」、などのケースも散見され、気合と根性と建前の世界になってしまっています。
例えば製造部門での、施策・改善アイテムの評価・更なる施策立案には以下が実施可能な仕組みが必要です。
- 前年の単価やロス率・能率(以下原単位)から改善を原単位別に立案する。
- 改善アイテムから予算原価を作成する。
- 予算原価と実際原価の分析を原単位別に実施する。
- 原単位別の予実差異から改善アイテムを評価する。
- 追加の改善アイテムを検討する。
【図3】施策・改善アイテムの評価・改善推進が可能な仕組み
単品実際損益・原価の見える化による計画の精度向上
上記の解決策は実際損益・実際原価が単品別(品目別)に把握できていることが前提となります。実際原価がグロスですと、計画反映は金額で「なんとなく前年から〇〇%」となりがちです。改善アイテムも「結果いくらくらいを反映すればいいだろう」となり、その結果も評価しきれずに改善活動もなりゆきになりがちです。単品の実際損益・原価を把握することで初めて単品レベルの意思入れができることになり、根拠のある改善アイテム立案・評価が可能になります。
将来を見通すには、まずは足元を固めるべきです。
【図4】意味のある計画実績管理と意味のない計画実績管理
本記事では、先行き不透明な現況下における短サイクル計画実績管理のポイントについて書かせていただきました。詳細は是非お問い合わせください。
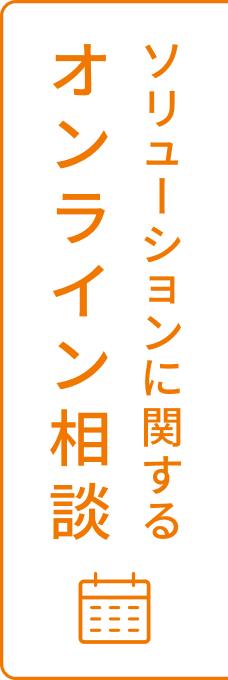
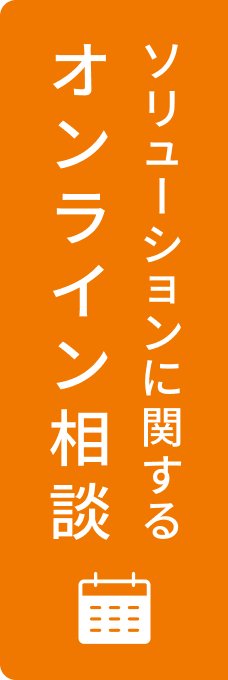
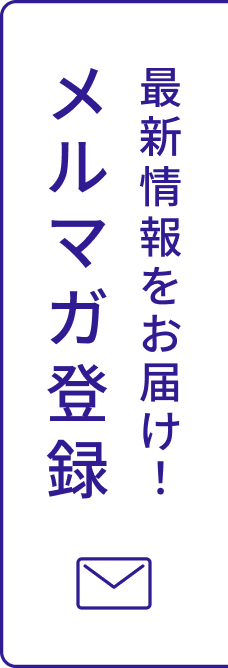
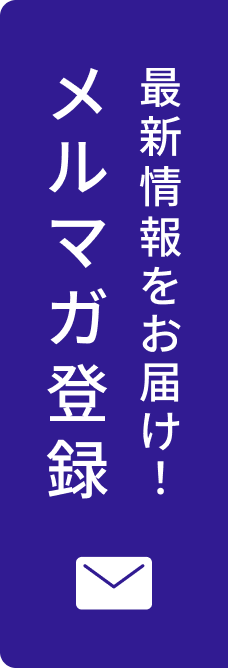
オンライン相談問い合わせる メルマガ登録
最新情報をお届け! メルマガ登録
この記事の執筆者
-
上山 吾郎経営管理事業部
マネージングディレクター -
佐藤 美穂子経営管理事業部
ディレクター -
徳永 大経営管理事業部
シニアマネージャー
職種別ソリューション