現場と経営をつなぐ実践的コストマネジメント
また、現場で取り組んだ改善活動と経営にて管理している指標のつながりが見えにくいため、現場・経営双方で不満が発生しています。
そこで、この不満を解決すべく
・適切に把握するための原価とはどのようなものなのか
・実績情報の習得など現場への負担が増えないのか
・算出された数値をどのように活用すべきなのか
といった原価に対する疑問について、「原価管理の実現ポイント」を交えながら解説いたします。
標準原価では視えない現場と経営の実態
現在、エネルギー高騰、為替変動、労働力の確保、サプライヤーの廃業と原価を上昇させる要因が多い状況で、原価が高くなった際に何が原因で原価が高くなったのか分かりづらくなっています。
また逆に、エネルギー費や為替といった各要因が、どの製品のどの工程に影響を与えたのかも分からなくなっています。このような状況下において標準原価で原価を把握することは、更に「正しい原価」が視えなくなってしまっています。その主な理由として、下記の4つがあります。
① 標準原価の改訂は年一回程度
② 原価差額が数パーセント発生(営業利益の半分程度の原価差異になっていることも)
③ 製造間接費は原価管理の対象外
④ 設計、販売、一般管理部門で工数把握に基づく原価管理をしていない
③④については、下記の図で解説します。
製造間接費は、一般的に製造原価の約3割と製品原価の中で占める割合が大きく、更に間接費は製品ごとに発生する費用が異なるにもかかわらず、製造直接費の比率で配賦されるため、製品に与える原価のインパクトも大きいにも関わらず製品ごとの違いが把握できません。
この図のケースですと、製品Aと製品Bは直接費が同じですので、間接費を直接費率で配賦すると同じ間接費額になってしまいます。また、設計、販売の費用も売上高比率で配賦されることが多いのです。
これでは直接費と同率の間接費になり、販管費についてはどの製品も同じ販管費率となるため、それ以上の分析がされません。これらの費用は、共通費として製品に共通的に配賦されてくるコントロールできない費用として扱われ、手を打つことなくそのままにされています。製品Bは工場間の移動が多い、設備の修繕が多い、電気の使用料が多く、開発時間も長く、営業活動の時間・人員数が多いといった原価を高める要素が分かっているのであれば、その実態を原価に反映すべきです。右の図は実態を反映した原価を表しており、結果製品Aと製品Bの原価は大きく異なることが分かります。
【図1】製造間接費・販管費の配賦イメージ
正しくない原価による管理は、経営層・現場の不満になる
正しくない原価で管理していると、経営層からは現場では改善しているという報告を受けているものの、損益改善額につながっていないという声をよく聞きます。
一方、現場では日々頑張って改善しているのに製品利益には反映されず、それ故、自分たちがどれだけ経営に貢献できているか分からないという声や、製造現場の実感と製品別原価が大きく乖離しているという声もよく聞きます。
つまり、両者とも改善につながっていない原価を見ていることが、この不満を発生させています。
製造現場は改善指標に基づいて改善をおこなっており、その結果として、原価にどれだけ影響したか、原価がいくらになったかを見せることがこの不満の解決策になります。
原価の変動要因ごとの金額が分からなくなっていたり、工場全体の金額では各工程の費用が相殺されたりするため、「実際原価による工程別の活動基準原価計算」で管理すべきです。
【図2】経営層・現場からの不満
不満の解消:製造現場の改善指標が評価できる仕組みづくり
先ほど述べたとおり、製造現場では改善指標に基づいた改善を日々行っています。
例えば、生産にかける時間を増やすために、作業の習熟度を上げ作業能率を上げたり、機械の不具合による停止時間をなくすようにしたり、生産計画を見直して設備の稼働率を向上しています。また、段取り作業についても内段取りから外段取りに変えたり、そもそも段取りが最小限になるような生産計画を考えたりしています。
この改善活動がどの製品のどの工程に影響を与え、金額としてどのくらい低減できたかを視える化することが不満の解消になります。製造現場では改善した分が数値に反映されるため、どれだけ利益に貢献できているかが分かりモチベーションが上がります。
また、経営層も製品の原価低減額が評価できるようになるため、お互いに納得感があります。このような改善活動を経営層が評価できる金額にする仕組みがあれば、製造現場で原価低減のアイデア出しをした後、実際にシミュレーションすることで目標値に足りているか確認したり、優先順位付けをすることも可能になります。
製造現場の改善活動が製造原価のどの工程・費目に影響があり、結果的に、製造原価がいくらになっているかを分かるようにするには、改善活動と工程・費目を紐づけることが必要です。
ただ、工程や費目を細かく分ければよいということでありません。現場の改善活動につながるものを中心に紐づければ良く、改善活動が例えば労務費、経費、間接材料費のどれにつながるのか分からない場合は、直接費や間接費といったように費目をまとめても構いません。
【図3】改善活動と製造原価
実際原価管理が浸透しない理由とその対処法[1]
実際原価による管理が重要なことは理解していただいたと思いますが、なぜ実際原価管理が浸透しないのでしょうか。その理由は大きく2つあります。
1つ目の理由は、新たに実績を把握することが製造現場の担当者の負担増となるということです。
実際原価管理に必要十分な実績データを網羅的に取得・管理できている企業は多くありません。せっかく原価管理のロジックを考えてもその原単位の情報が取れなくては意味がなく、手作業で実績収集をするとなると逆に現場に負担がかかることになり長続きしません。
その解決策として、DXの活用があります。
DXの進展により、担当者に負担をかけず原単位情報を収集することが可能になっています。
例えば、工程監視カメラで作業時間を記録したり、設備の稼働・停止時間を設備側から自動把握したり、ウェアラブル機器によって作業の履歴管理を記録することができます。
また、全ての工程でDXを活用するのではなく、管理上重要な(=改善可能な)工程でのみ活用するなどメリハリをつけることでDXのコストも抑えられます。
あるメーカーでは、不良情報の入力について手間やミスが多かったため、設計情報を現場のタブレットに取り込み、どの箇所で不具合があったかを画面上で指定し、不具合や手直し情報を記録することで精度と負荷軽減の両立を実現しました。
【図4】工程の特性に応じた現場DXツールの活用
実際原価管理が浸透しない理由とその対処法[2]
2つ目の理由は、先に課題としてあげましたが、コスト改善努力が現場にも経営層にも見えず、評価しにくいことがあります。改善活動に紐づいた製品別の実際原価計算を行うことで、製品別原価の低減金額が分かるようになります。しかし、そこで見ている原価はあくまでも製品単位のため、製品・工程別の原価を製品群別、組織別・工場別と集約することで工場長が管理している指標につなげ、またそれを事業別に集約することにより経営層の管理している指標につなげることが重要です。
また、現場の改善活動から事業別P/Lに集約するだけでなく、下記の図にあるように、経営からも事業別P/L(利益)から工場や現場の管理している原価へと製品原価を軸にブレイクダウンを可能とすることも必要であり、この「経営と現場をつなげる仕組みづくり」が実際原価管理の定着には必須です。経営・工場・現場とこれらの情報をアウトプット帳票やダッシュボードで共有することで、同じ目標・結果も共有でき、経営層が現場の改善効果を適切に評価できるとともに、現場が “利益貢献”を意識した活動を行うことができるようになります。
【図5】経営(会社/事業/製品の損益)と現場をつなぐ仕組みづくり
まとめに
原価管理のプロジェクトでは、生産の課題や生産・製品の特徴を踏まえながら、実際原価計算のロジック検討を行います。現場や経営層の思い・こだわりを反映した実際原価計算を策定しても、それが活用されないと意味がありません。実際原価計算を定着させるためには、①現場の負担をかけないこと、②活用できる仕組みづくりがポイントです。
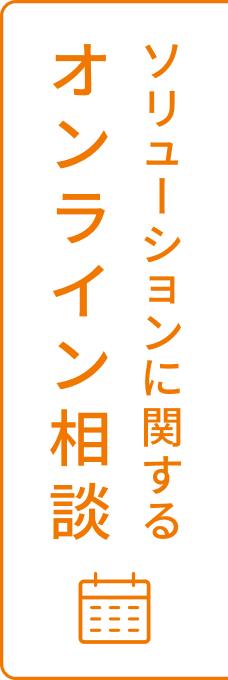
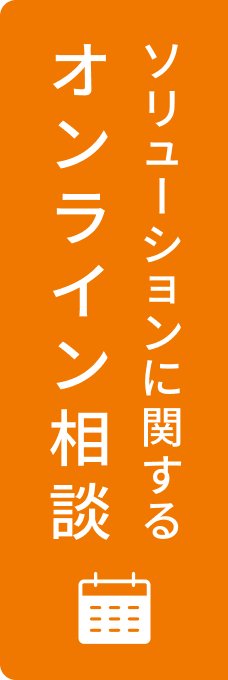
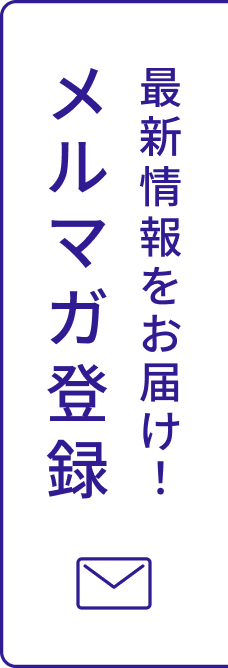
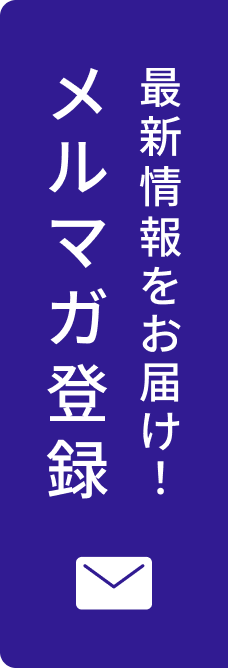
オンライン相談問い合わせる メルマガ登録
最新情報をお届け! メルマガ登録
この記事の執筆者
職種別ソリューション