ピンチこそチャンス
有事に強いサプライチェーン再構築のポイント
こういったことを踏まえると、不測の事態が起きることを前提として、普段から準備をしておくことが、持続的なサプライチェーン構築のための重要なポイントです。
本稿では、その準備として何をすべきかを記しております。将来の憂いを少しでも取り除くために今何をすればいいのか、そういった観点で読み進めていただけますと幸いです。
有事にむけて何を備えればいい?
有事のシナリオは、天災、疾病の流行、紛争や情勢不安と多岐にわたり、これらの有事がいつどこで起きるか、全て予測して事前に対処することは現実的にはあり得ません。よって、どのような環境変化が起きたとしても代替生産・調達できる、レジリエンスなサプライチェーンの構築が求められています。
加えて、生産性向上を常に求められる昨今、有事が起きた場合でも、納期遅延やコスト増加が許容されるわけではありません。特に日本企業は、コロナ禍においても納期を守っていたことが、あらためて国際的な評価を高める要因になりました。今後も国際的な競争を勝ち抜くためには、有事においても納期を守る、コストについても影響を最小限に抑える必要があります。レジリエンスなサプライチェーンの構築と生産性の追求を同時並行で行う必要があります。
そのためには、実際に不測の事態が起きてから対応する、ということでは実現は極めて困難です。
平時でも、「有事を想定したサプライチェーンの強化=備え」を行うことが重要となってきます。
具体的な備えとして、以下が挙げられます。
① モノづくりの仕組みの共通化
② キーコンポーネントの供給確立
③ 製品の絞り込み
それぞれのポイントについて、次章以降でご説明します。
【図1】代替生産・調達は平時からの準備が重要
平時の備え① モノづくりの仕組みの共通化
モノづくりの仕組みが工場毎に異なっていては、いざという時に代替生産・調達ができない、できたとしても準備に大きく時間を要することになってしまいます。これでは、納期遅延やコストアップを招いてしまいます。生産・調達の代替を円滑に進めるためには、生産プロセスや部品の共通化を平時から進めておくことが必要です。共通化が求められるものとして、以下の2つが挙げられます。
(1)生産領域における共通化の推進-生産領域:設備・工程・治工具
(2)調達領域における共通化の推進-調達領域:部品・ルート
(1)生産領域における共通化の推進
生産領域における共通化は、まず生産ラインで必要となる機能を明確化・整理することから始まります。その上で、細分化した機能をもとに設備に求められる仕様を明確化、設備モジュールとして機能を分けて開発します。これにより、設備モジュールには各製品の生産工程に必要な機能が盛り込まれ、通常は製品Aを製造する設備で、別の製品Bの製造も可能となります。
設備モジュールの組み合わせで工程を定義し、生産ラインを構築します。これをグローバルで統一したモデルとして定義することで、グローバルでのモノづくりを共通化することが可能となります。ある工場で問題が起きたとしても、他工場で同一の品質と効率を維持した形で代替生産ができる設備・生産ラインを保持することが可能となります。
【図2】生産ライン・設備の共通化の進め方
(2)調達領域における共通化の推進
調達面でも、要求仕様を軸に調達部品を工場・事業を超えて共通化することで、部品点数をスリム化できます。その上で、部品毎にマルチサプライヤ化を進め、有事が起きた場合でも複数の調達ルートを確保することが望ましいです。 そして、これらの共通化を推進するにあたっては、品目やBOM、そしてサプライヤの技術情報を工場間で互換性のある形で連携し、最新状態を保つことも併せて求められます。
平時の備え② キーコンポーネントの供給確立
前項で代替生産の重要性に触れましたが、製品の性能を左右する独自の技術を盛り込んだキーコンポーネント部品はどこでも生産・調達できるわけではありません。自社の技術を織り込んでいるため、自社の中でも特定の工場から供給されるケースがほとんどです。そのため、当該工場で有事が発生した場合、供給が途絶えるリスクが高く、他工場を含めた生産活動に大きな影響を及ぼしかねません。 こうした事態を未然に防ぐため、自社におけるキーコンポーネントに該当する部品は何か、製品の構成部品を踏まえて整理・抽出することが必要です。抽出のポイントは、以下の2つが挙げられます。
(1) 他社との差別化を可能にしている部品
(2) 自社製品の中で多数で使用されている部品
(1)他社との差別化を可能にしている部品
他社との差別化を生み出す部品とは、もちろん自社独自の技術を持ち、性能的に優位になる部品を指します。ただし、そういった性能差だけではなく、安定した品質で部品を供給し続けることができる、他社と比べて低価で製造することができるといった点を含めて、自社にとっての差別化要因を持つ部品が、キーコンポーネント部品になると考えます。
(2)自社製品の中で多数で使用されている部品
多くの製品で共通的に使用されている部品は、供給が停止してしまうと波及範囲が大きくなってしまいます。そのため、そういった共通品についても、キーコンポーネント部品として扱うことが必要と考えます。 こういった部品を抽出するためには、自社製品のBOM情報を整備しておくことが重要です。BOMをもとに多くの製品に組み込まれている部品を選定し、該当する部品から優先的に供給が停止しないような仕組みづくりや、共通部品の度合いをコントロールする施策が必要となります。
平時の備え③ 製品の絞り込み
ここまで紹介してきた有事への備えを効果的に行うためには、製品の絞り込みが重要です。
特に日本のメーカーは、顧客ニーズにきめ細かく応えるために、多彩な製品展開をしている企業も多いですが、製品バリエーションが多いと工程・設備・部品の種類が増え、対策に時間とコストがかかります。
その結果、迅速な対応が難しくなり、モノづくりの仕組みの共通化や、キーコンポーネントの供給確立の効果が低減します。
一方、経年とともに製品は増えていき、その中には、機能や性能が重複する製品や、需要が薄れたものも散見されます。これをスリム化したいと思っても、ラインナップや売上減少の懸念や、顧客との関係性から、なかなか踏み切れないことが多いです。しかしながら、仕様統合の取り組みによって、モノづくりの仕組みの共通化や、キーコンポーネントの供給確立の効果が大きく発揮され、企業の競争力を維持し、安定した供給体制を構築することにつながります。この取り組みは製造部門だけでは推進できないので、営業部門との意識共有・理解も必須となります。
絞り込みの方法としては、以下2つがあり、それぞれ当社ご支援事例を交えてご説明します。
(1)仕様統合による絞り込み
(2)原価・利益観点での絞り込み
(1)仕様統合による絞り込み
実際の受注をもとに必要な所要量を見極め、仕様統合の可能性を評価します。電子部品メーカーのご支援事例では、所要量から顧客が求める仕様を可視化し、社内で必要と考えている仕様とのギャップを明らかにした上で、必要な仕様の絞り込みを行いました。加えて、似たような機能で重複する仕様を整理し、統合を試みました。その結果、既存製品の1割を削減し、基準仕様を採用することで3割の部品を削減することが可能となりました。
【図3】製品絞り込み事例(1)~仕様統合によるアプローチ~
(2)原価・利益観点での絞り込み
製品毎に原価を算出して、製品毎の利益を評価します。そして、利益の低い製品は価格変更(値上げ)や終売を行うことで、経営資源を高利益の製品に集中させます。自動車部品メーカーのご支援事例では、製品毎の実際原価の試算を実施しました。その結果、売上下位20%の製品が営業利益の25%を食い潰していることが判明し、販売部門も巻き込んで価格調整や終売を行いました。
【図4】製品絞り込み事例(2)~原価・利益管理によるアプローチ~
まとめ
本稿では、有事に向けた具体的な取り組みについてご紹介してきました。それぞれの取り組みは、仮に有事の事態が起きなかったとしても無駄になるものではなく、自社の生産性向上、柔軟な生産体制の構築等に寄与するものと考えています。
ご紹介した取り組み自体は、一朝一夕で進められるものではありません。
平時の時から計画を立て、着実に推進していくことが求められます。
関連サービス
#サプライチェーンマネジメント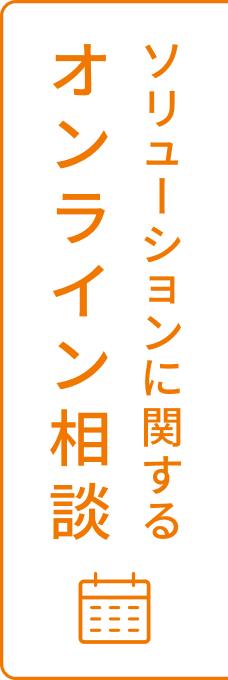
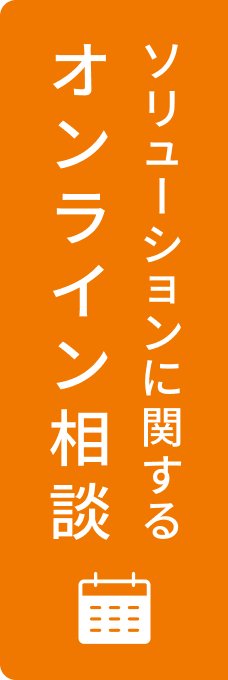
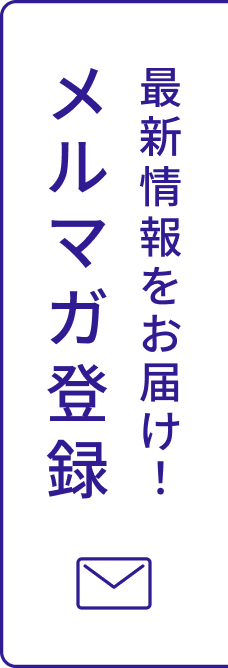
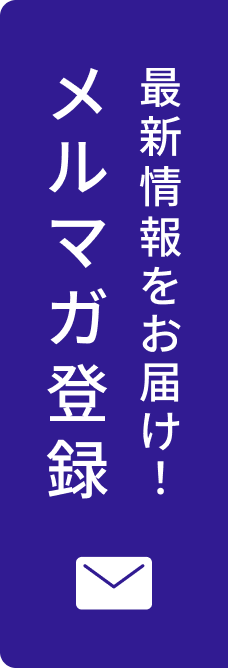
オンライン相談問い合わせる メルマガ登録
最新情報をお届け! メルマガ登録
この記事の執筆者
-
竹森 政弥SCM事業部
マネージングディレクター -
赤堀 和樹SCM事業部
マネージャー
職種別ソリューション