2025/02/14
物流2024問題から1年、どんな手を打つべきか? ~物流DXによる改革アプローチ~
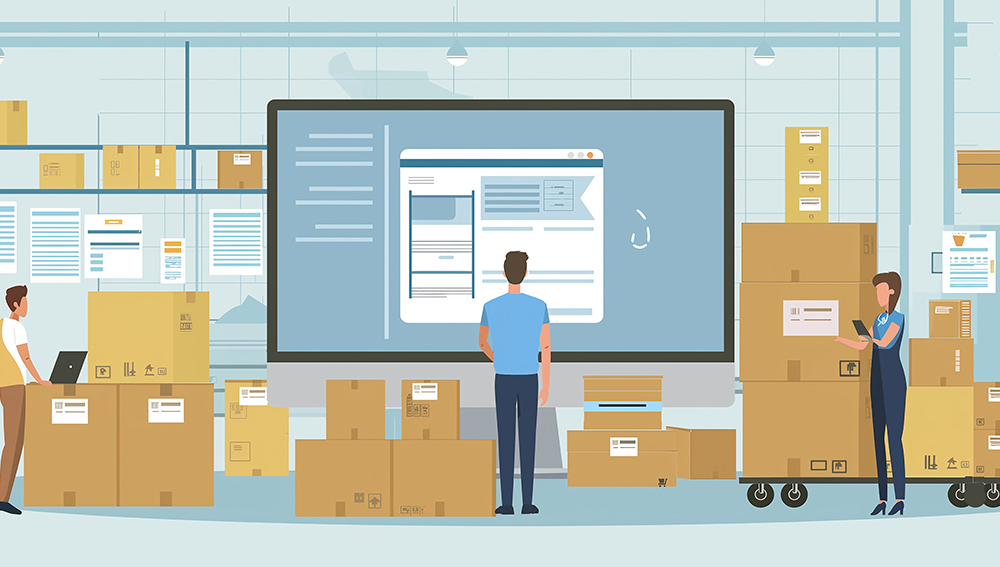
今回は、企業の物流課題を振り返るとともに、「物流2024問題」から脱却する足掛かりとなる改革アプローチの基本をご紹介します。
物流2024問題とは?
働き方改革関連法の改正および厚生労働省の改善基準告示に伴い、2024年4月1日よりトラックドライバーの労働時間、拘束時間が規制されるようになりました。これによりトラックドライバーの年間時間外労働時間の上限が960時間に制限されるほか、ドライバーの運転時間や休息時間にも制約を課すことで、長時間労働が常態化しているトラック運送業界の労働環境を改善させることを求められています。
また、今回の法令改正は自動車運転業務を含む一部業務に対して960時間の制限が設けられましたが、将来的には一般則と同基準となる年間720時間の制限が適用されることが見込まれており、運送業界に更なる改革が必要になります。
参考:厚生労働省 働き方改革を推進するための関係法律の整備に関する法律(平成30年法律第71号)の概要
参考:厚生労働省 自動車運転者の労働時間等の改善のための基準(改善基準告示)
参考:公益社団法人秋田県トラック協会 労働関係法令改正に係るリーフレット
参考:公益社団法人全日本トラック協会 知っていますか?物流の2024年問題
参考:国土交通省 東北運輸局 物流の「2024年問題」とは
企業が直面している物流課題
物流コストが増加
トラックドライバーの拘束時間が減少することにより1日当たり/1人当たりの輸送力が低下するため、これまでの輸送力を確保するためにも、ドライバーの増員などの物流コストが増大してしまいます。
加えて、昨今のトラック運送業界の慢性的な人手不足からドライバー確保のための賃金アップも必要となり、物流コストの増加に拍車をかけている状況です。
短納期・長距離輸送、緊急対応が不可
ドライバーの労働時間の制限、およびそもそもの人手不足の環境において、これまでのような短納期・長距離輸送、あるいは緊急対応を受けられなくなる運送事業者も現れることが予想されます。
これまで通りにモノが届かない/届けられないケースも発生し、物流をサプライチェーンの調整弁としていた企業活動が成立しなくなることも考えられます。
物流2024年問題に対応しようにも課題が山積み
上記のような課題に直面している一方、これまで現場任せで物流の効率化・改善に注力してこなかったために、物流2024年問題に有力な打ち手を見出せていないケースもあります。
- トラックの配車・積載状況が可視化されておらず、自社の物流計画・物流コストが適正か判断できない、効率化を図るノウハウがない。
- 営業拠点・生産拠点・物流拠点それぞれにおける入出庫・保管・横持のような業務がマンパワー頼りで効率化(自動化・無人化など)できてない。
物流業界における基本的な改革アプローチ
適時適量配送
お客様が求めるものを、必要なタイミングで、必要な分だけお届けするということが物流の基本です。
ただし、どうしても即納できない品物もあります。その場合はいつお届けできるか納期をお知らせすることが重要です。業界によっては「即答率」というKPIで管理しています。
これまで特に日本では「早ければ良い」という考え方があり、当日に受注したものは翌日にはお届けするといった体制を多くの業界で構築してきました。本当に翌日に届ける必要があるのか?ということについてはあまり深く考えてはいないのではないでしょうか。
物流2024問題が注目され、ドライバー不足や待機時間の規制について多くの企業で検討を開始しております。これまでの常識(即納体制)にとらわれていては立ち行かないということを改めて認識し、抜本的な改革に着手されています。即日ではなく、2日に1回でも問題ないのではないか?お客様起点で本当に必要な在庫配置や最適在庫は何か?について改めて見直しを行っています。
即納、即答の考え方(適切な在庫戦略)
多くのメーカーでは需要予測を行い、商品の流動性に応じて在庫を保持し、日々お客様からいただく受注に対して欠品が起きないように生販在の管理を行っています。
- 即納、即納率
在庫を常に切らさず、お客様からの注文に対して即時出荷をできるようにすることを「即納」と言います。「即納」の対象品は主に高流動品や業界によっては重要保安部品等、絶対に欠品を起こしてはいけないものを対象としています。
「即納率」=サービスレベルととらえている会社も多く、KPI管理の対象としています。ただし、何でもかんでも在庫を持つとなると、在庫コストが非常にかかるため、何を持つべきかを判断する適切な在庫基準が必要になります。
- 即答、即答率
「即答」は手元に在庫は無いが、納期を示すことができる状態を表します。納期を明示できれば、お客様はいつ商品が届くのかわかるため、我々一般消費者からの問い合わせにも明確に答えることが可能になります。
実はこれが結構大変で、実現するためには、商品ごとの各種リードタイムを決めておくことが必要で、さらにそれらを元に納期を自動計算し、関係者と共有できる情報システムが必要になります。
ハブ&スポーク
ハブ&スポークとは、物流や情報技術分野など、様々な場面で使われる用語です。
自転車の車輪をイメージするとわかりやすいと思います。中心のハブから、スポークと呼ばれる棒が放射状に伸びて外側の輪を支えています。この構造と同様に、ハブ&スポークは、中心となる拠点(ハブ)に物や情報を集め、そこから各拠点(スポーク)へ分岐させて運ぶ仕組みを指します。
物流の場合、宅配便会社が全国の荷物をまず地域のハブに集め、そこから各地域の配送センターへ振り分ける仕組みが具体例としてわかりやすいと思います。
ハブ&スポークのメリットは以下の3点です。
- 効率的な輸送: 複数のルートを一本化することで、輸送回数を減らし、時間とコストを削減できます。
- スケールメリット: ハブに集約することで、大規模な仕分けや保管が可能になり、スケールメリットを生み出せます。
- ネットワークの構築: 複数の拠点をつなぐネットワークを効率的に構築できます。
一方、ハブ&スポークのデメリットは以下の通りです。
- ハブに集中するため、ハブが故障した場合にシステム全体が停止するリスクがあります。
- ハブまでの距離が遠くなる場合、輸送時間が長くなります。
- ハブの容量に限りがあります。
フィジカルインターネット
フィジカルインターネットとは、トラック等が持つ輸送スペースと倉庫が持つ保管・仕分スペースのシェアすることで物流全体のリソースの稼働率を向上させることを指します。より少ない台数のトラックで荷物を運ぶことで地球温暖化ガス排出量を削減し、持続可能な社会を実現するための物流のコンセプトです。
「インターネット」のパケット交換の仕組みを物流に適用して、「フィジカル」なモノの輸送・仕分・保管を変革することから、フィジカルインターネットと呼ばれています。
物流のシェア
物流をシェアする方法は、近年、物流業界の効率化やコスト削減のために注目されている取り組みです。以下に、代表的な物流シェアリングの方法をいくつかご紹介します。
1. 倉庫スペースのシェア
- 空きスペースの有効活用:倉庫を所有している企業が、自社の利用状況に合わせて余剰スペースを他の企業に貸し出すことで、スペースの有効活用と収入の増加を両立させます。
- 共同利用型倉庫:複数の企業が共同で倉庫を建設・運営し、スペースをシェアすることで、初期投資を抑え、最新設備を共同で利用できます。
2. 配送車両のシェア
- 共同配送:複数の企業が同じ地域へ配送する場合、車両を共同利用することで、積載率の向上と配送コストの削減を実現させます。
- トラックシェアリングプラットフォーム:スマートフォンアプリなどを活用し、荷主と運送事業者をマッチングさせるプラットフォームを通じて、空車車両の有効活用を促進できます。
3. 物流情報のシェア
- 物流プラットフォーム:複数の企業が共通の物流プラットフォームを利用することで、リアルタイムな輸送状況の共有や、在庫管理の効率化を図ることができます。
- ブロックチェーン技術:ブロックチェーン技術を活用することで、物流情報の透明性・信頼性を高め、サプライチェーン全体の効率化に貢献できます。
4. 人材のシェア
- ドライバーシェアリング:ドライバー不足に対応するため、複数の企業でドライバーをシェアする仕組みを構築します。
- 人材派遣:人材派遣会社を通じて、必要な時に必要なスキルを持った人材を調達することができます。
物流シェアのメリット
- コスト削減:倉庫や車両などの固定費を削減し、スケールメリットを享受できます。
- 効率化:共同配送や情報共有を通じて、配送ルートの最適化や在庫管理の効率化を実現できます。
- 環境負荷の軽減:共同配送による車両の削減や、空車運行の減少を通じて、CO2排出量の削減に貢献できます。
- 柔軟な対応:需要の変動に合わせて、迅速かつ柔軟に物流リソースを調整することができます。
物流シェアリングの課題
- 情報セキュリティ:複数の企業が情報を共有するため、情報漏洩のリスクが高まります。
- 信頼関係の構築:複数の企業が協力して物流シェアリングを行うためには、相互の信頼関係が不可欠です。
- 法規制:物流シェアリングに関する法規制が未整備な部分もあり、法的リスクが存在します。
物流シェアリングの今後の展望
物流シェアリングは、IoTやAIなどのテクノロジーの進展とともに、ますます高度化していくことが期待されています。例えば、ドローンやロボットを活用した配送システムの導入や、AIによる需要予測に基づいた最適な物流計画の策定などが考えられます。
物流シェアリングは、物流業界の課題解決だけでなく、サプライチェーン全体の効率化や、持続可能な社会の実現に貢献する重要な取り組みです。
物流DXを支えるソリューション
配送計画最適化AI
交通情報や天候情報、配送先情報等を活用してAIによる最適な配車オーダー・配送ルートを計算するソリューション・サービスが展開されています。車両情報や荷役・納品時間等を制約条件として設けることでさらに精度を向上させ、燃料消費量の削減や配送時間の短縮による物流コストの削減が可能となります。
<配送計画最適化AIのソリューション例>
- LYNA 自動配車クラウド(株式会社ライナロジクス)
- ZENRIN ロジスティクスサービス(株式会社ゼンリン)
- wise systems(三菱ふそうトラック・バス株式会社)
IoTを活用したリアルタイムトラッキング
先述したフィジカルインターネットを推進するためにも、IoT技術の活用が求められています。GPS情報やセンサーからのデータを用いて、輸送中の商品をリアルタイムで追跡することで、何が/どこに/どのような状態にあるか把握できるようになります。
<物流IoTのソリューション例>
- LADOCsuite(東芝デジタルソリューションズ株式会社)
- 物流業向けIoT・RFIDソリューション(TOPPANエッジ株式会社)
ドライバーシェアリング
配送会社の空き時間を活用して、複数の荷主企業でドライバーをシェアするプラットフォームが広まりつつあります。最短15分~1時間程度で配車が行える事例もあり、荷主企業の緊急対応に応えつつも配送会社の稼働率向上にも繋げられます。
<ドライバーシェアリングのソリューション例>
- ハコベル(ハコベル株式会社)
- トラボックス(トラボックス株式会社)
共同配送マッチング
自社の配送量や配送ルート、配送条件を登録することで、AIを用いた共同配送相手をマッチングさせるサービスが展開されています。日々の配送計画の最適化はもちろん、需給変動によって発生する非効率な配送を荷主企業間でマッチングすることで物流コスト低減に繋げることが可能です。
<共同配送マッチングのソリューション例>
- TranOpt(日本パレットレンタル株式会社)
- 共同配送マッチングLOG(株式会社Logpose Technologies)
物流業界におけるDXの取り組み事例(物流2024問題の対策)
製薬メーカーにおける調達物流改革
物流2024年問題に起因して出荷物流だけでなく、調達物流の改革に取り組む企業が増えてきています。これまで調達物流はサプライヤーが負担するもので、メーカー側は納期と数量を指定するだけで内容についてはタッチしてこなかった領域でした。昨今、物流2024年問題に起因してサプライヤーからの値上げ要請やドライバーの稼働時間の見直し通告(ex.ばら積みの禁止)が増えており、抜本的な業務の見直しが求められています。
あるメーカーでは、これまでサプライヤーが担っていた調達物流業務(荷揃え、出荷)をについて、サプライヤーが出荷するのではなく、メーカー側が引き取りにいくやり方に切り替えていこうとしています。狙いは“手の内化”です。調達物流機能を一旦サプライヤーから切り離し、メーカー側の視点で場所、物量、タイミングを組み直していき、受入側(工場)にとって最も効率的な納入方法を検討します。これまで全国200社以上のサプライヤーからそれぞれバラバラに納入されていましたが、各地域で集約し満載にして工場まで運んでくる方法に変更しました。これにより、便数の削減はもちろんのこと、工場の荷卸し待ちの時間の短縮にもつながり、物流2024年問題の解消にもつながります。
サプライヤーから調達物流を切り離すということは、調達物流単価(パレット一枚当たりの輸送費など)をメーカー側で管理することになります。当然、これまで材料の購入単価に含まれていた調達物流費相当分についてはサプライヤーと交渉して値下げしていただくことになります。また、調達物流費としてのコストテーブルをメーカー側で管理することになるため、仮に調達物流(輸送)を3PLなどへ外部委託する際にも適切な単価交渉が可能になります。
手の内化のポイントは、メーカー視点でサプライチェーン改革を推進できる領域を広げるということです。例えば、3PLと協力して全国の調達物流ネットワークを大胆に変更することも可能ですし、工場の受入荷姿に合わせた積み替えポイントを自由に設定することもできます。また、手の内化を進めることによって、実は副次的効果としてCO2排出量の削減といった社会的要請への対応にも寄与する取り組みになっています。